Wo es um das Weitergeben von Impulsen und Energie oder um das Festhalten geht, sind sie gefragt: Rasten und Hebel sind für Komplikationen unverzichtbar. Heutzutage werden sie mittels Drahterosion hergestellt – einem zunehmend wichtigen Verfahren für die Uhrenindustrie.
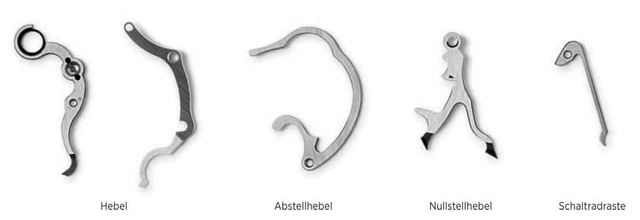
Rasten und Hebel: Diese Kleinteile stammen aus dem Handaufzugskaliber L903.0 des »Tourbograph Pour le Mérite« von A. Lange & Söhne und wurden mittels Drahterosion hergestellt.
PR
Sie sehen genauso aus, wie man sie sich vorstellt: Der Name Hebel passt perfekt zu diesen Uhrwerkkomponenten. Sie sind länglich, schmal und bisweilen abgewinkelt geformt. Dabei verdanken diese Teilchen ihren Namen nicht ihrem Aussehen, sondern ihrer Funktion. Hebel wirken als Überträger von Kraft und Bewegungen. Eigentlich sind sie nicht mehr als um eine feststehende Achse drehbare Stangen. Hebel sind nicht nur im Schlagwerk- und im Chronographenmechanismus zu finden, sondern erfüllen ihre Aufgabe auch als Stellhebel, Kupplungs- und Winkelhebel.
Die Hebel eines Uhrwerks erfüllen verschiedene Aufgaben
Der oft rechtwinklig ausgebildete Winkelhebel hat seinen Platz im Aufzugmechanismus. Er gibt den Zug an der Krone und damit an der Aufzugswelle an den Kupplungshebel weiter. Dadurch kommt das Kupplungstrieb in Eingriff mit dem Zeigerstellrad, was die Zeigerverstellung schließlich möglich macht. Weitere Beispiele sind der Schlagauslösehebel sowie der Herzhebel. Ersterer kommt in Schlagwerken zum Einsatz, wo er normalerweise das Räderwerk blockiert. Wird der Auslösehebel durch einen Auslösestift oder -stern angehoben, so ist das Räderwerk frei zum Schlagen. In Repetitionsmechanismen hat der Auslösehebel eine bestimmte Form, die dafür sorgt, dass das Schlagwerk nur dann schlägt, wenn der Hebel ganz bis zum Anschlag geschoben oder gedrückt wird, was als "Alles oder nichts"- beziehungsweise "Tout ou rien"-Prinzip bezeichnet wird.Der Herzhebel ist Teil des Chronographenmechanismus
Der Herzhebel ist hingegen Teil des Chronographenmechanismus. Seine Aufgabe ist es, die Räder für Sekunden- und Minutenzählung nach dem Stoppvorgang in ihre Nullposition zu bringen. Ist der Stoppvorgang beendet, wird durch Betätigen des entsprechenden Drückers der Herzhebel von einer kräftigen Feder in Bewegung gesetzt. Die Schaltflanken des doppelarmigen Herzhebels treffen dabei auf zwei herzförmige Kurvenscheiben, die so genannten Herzen.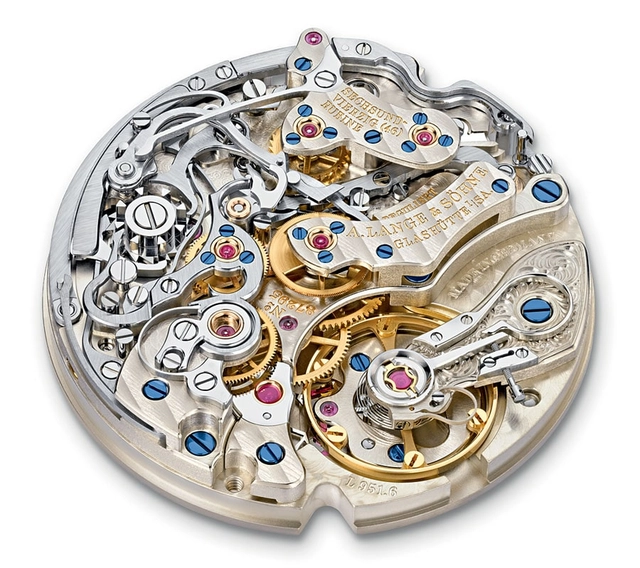
In das Kaliber L951.6 von A. Lange & Söhne mit Schaltrad-Chronograph sind Herzhebel eingebaut
PR
Dadurch werden die Zählräder blitzschnell gedreht und angehalten, wenn das der Herzspitze entgegengesetzte Ende, die so genannte Kerbe, an der Schaltflanke des Herzhebels anliegt. Die Chronographenzeiger bleiben nun auf null stehen, vom Herzhebel bis zur nächsten Auslösung des Chronographen blockiert. Auch anhand der Lange 1 Zeitzone von A. Lange & Söhne lässt sich die Tätigkeit eines Hebels beispielhaft beschreiben. Wird der Drücker zum Weiterschalten des Städterings betätigt, drückt er auf einen Hebel, dieser auf eine Klinke. Die Bewegung trifft auf einen Viererstern, der mit einem 32-zahnigen Rad vernietet ist und schließlich den Städtering mit 192 Zähnen um acht Zähne beziehungsweise eine Stadt weiterdreht.
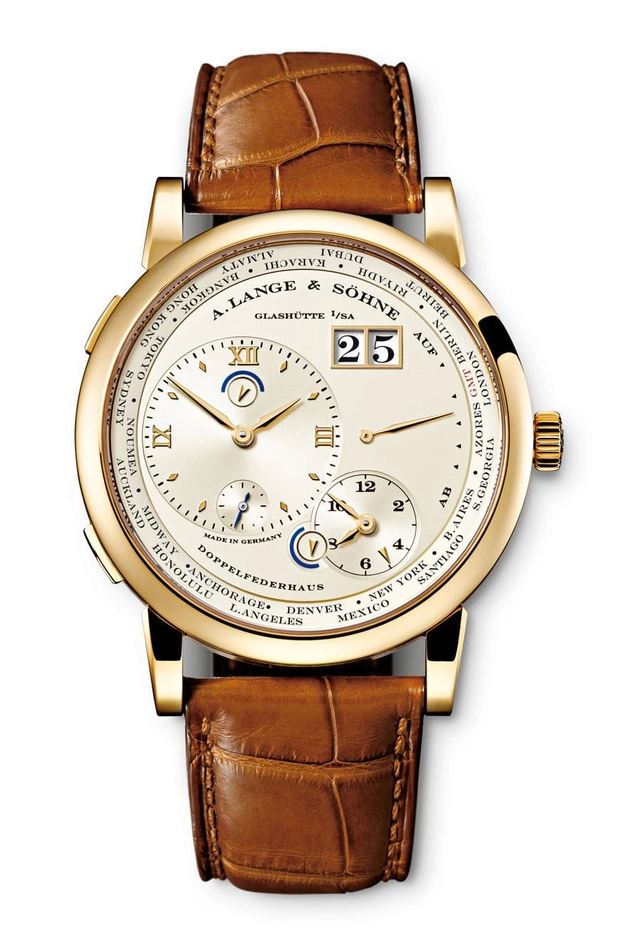
Lange 1 Zeitzone in Gelbgold von A. Lange & Söhne
PR
Nicht weniger wichtig sind Rasten, die im Uhrwerk ebenfalls in verschiedenen Formen zum Einsatz kommen. Ihre Aufgabe ist es, ein anderes Bauteil, zum Beispiel ein Rad, zu fixieren – in Zusatzmodulen wie Datum, Großdatum oder ewiger Kalender, also vorwiegend in Schaltmechanismen. Denn in diesen müssen Schaltsterne oder Räder dadurch fixiert werden, dass Rasten entsprechend in den Zahnzwischenraum drücken. Die Rasten können sowohl als Feder oder auch als drehbar gelagerter – wiederum von einer Feder beaufschlagter – Hebel ausgeführt sein. Die gewählte Ausführung hängt überwiegend von den gegebenen Platzverhältnissen ab, die Wirkung ist unabhängig davon die gleiche. In den Uhrwerken von A. Lange & Söhne findet man beide Varianten, bevorzugt wird allerdings nach Möglichkeit die zweite, da sie insgesamt wertiger erscheint.
Die Rasten fixieren die Teile eines Uhrwerks
Beim Weiterschalten wird die Raste aus der eingenommenen Raststellung herausgedrückt. Nach Vollendung des Schaltvorgangs fällt sie in die nächste Zahnlücke und fixiert den betreffenden Schaltstern oder das Rad bis zur nächsten Weiterschaltung. Die Rastkraft muss so gering sein, dass sie überwunden werden kann; gleichzeitig muss sie aber ausreichend groß sein, um die Bewegung des Schaltsterns beziehungsweise des Rades zu vollenden und bis zur nächsten Weiterschaltung sicher zu halten. Diese Abstimmung der Kräfte erfolgt meist durch mehrere Versuche. Dazu wird eine zu Beginn bewusst zu stark gewählte Feder immer weiter abgeschliffen, bis die Abstimmung passt. Die gängige Herstellungsmethode für Rasten oder Hebel ist Stanzen. Dabei werden die Metallelemente unter Druck auf einer Presse mit scharfrandigen Stempeln ausgeschnitten. Auch andere Uhrwerkteile wie zum Beispiel Platinen, Brücken und Zahnräder werden ausgestanzt und je nach Wertigkeit des Uhrwerks und dem selbst gestellten Anspruch des Herstellers manuell nachbearbeitet.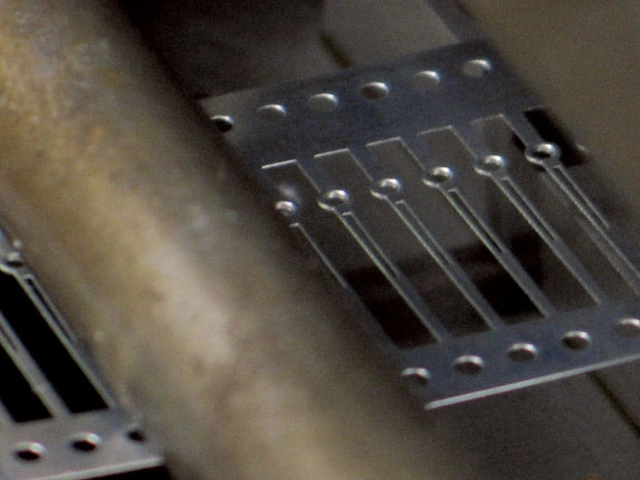
Serienproduktion: Das Stanzen aus einem Metallband eignet sich nur bei großen Stückzahlen. Hier die Fertigung von Zeigern.
PR
Die Stempel für die Form des herzustellenden Teils werden von ausgebildeten Werkzeugbauern angefertigt und sind anschließend jeweils nur für dieses eine Bauteil zu verwenden. Viel Aufwand, der teuer zu bezahlen ist. In der Haute Horlogerie, wo nur relativ kleine Stückzahlen benötigt werden, lässt sich dieses Verfahren kaum kostendeckend einsetzen. Während bei Massenproduktionen das Stanzen in jeder Hinsicht am günstigsten ist, steigen viele Firmen bei der Fertigung kleiner Stückzahlen auf ein anderes Herstellungsverfahren um. Beim Schneiden mittels Drahterodieren wird mit einem Draht und elektrischer Entladung ähnlich einer Laubsäge eine programmierte Kontur in ein Werkstück geschnitten.
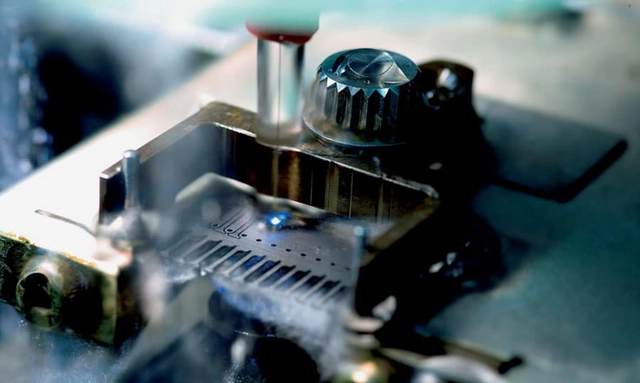
Funkenflug: Bei der Drahterosion wird Metall mittels polarisierter Spannung zwischen Erodierdraht und Werkstück geschnitten. Dabei springt mehrere tausend Mal pro Sekunde ein bis zu 25.000 Grad heißer Funke über.
PR
Der nur 0,02 bis 0,33 Millimeter dicke Erodierdraht besteht in der Regel aus Messing, beschichtetem Messing, Stahl oder Wolfram. Bei A. Lange & Söhne wird überwiegend mit einem 0,1 Millimeter dicken Draht gearbeitet. Das entspricht etwa der doppelten Dicke eines menschlichen Haares. Im oberen Teil der Erodiermaschine sind etwa 50.000 Meter Draht auf eine Spule aufgewickelt. Der Draht wird von dort über mehrere Umlenkrollen durch das Werkstück gezogen und danach entsorgt. Der Erodiervorgang beginnt am Werkstückrand oder in einer Startlochbohrung, durch die der Draht eingefädelt wird. Der Draht ist positiv gepolt, das stählerne Werkstück ist negativ gepolt.
Beim Drahterodieren werden die Werkstücke durch elektrische Entladung bearbeitet
Der nur 0,02 bis 0,33 Millimeter dicke Erodierdraht besteht in der Regel aus Messing, beschichtetem Messing, Stahl oder Wolfram. Bei A. Lange & Söhne wird überwiegend mit einem 0,1 Millimeter dicken Draht gearbeitet. Das entspricht etwa der doppelten Dicke eines menschlichen Haares. Im oberen Teil der Erodiermaschine sind etwa 50.000 Meter Draht auf eine Spule aufgewickelt. Der Draht wird von dort über mehrere Umlenkrollen durch das Werkstück gezogen und danach entsorgt. Der Erodiervorgang beginnt am Werkstückrand oder in einer Startlochbohrung, durch die der Draht eingefädelt wird. Der Draht ist positiv gepolt, das stählerne Werkstück ist negativ gepolt.Beim Drahterodieren werden die Werkstücke durch elektrische Entladung bearbeitet
Über eine pulsierende, polarisierte Spannung zwischen dem Erodierdraht und dem Werkstück entsteht ein starkes elektrisches Feld. Durch den geringen Abstand springt mehrere tausend Mal pro Sekunde ein extrem heißer Funke auf das Werkstück. Fachleute sprechen von 5.000, zum Teil gar von bis zu 25.000 Grad heißen Funken. Wo diese auf das Werkstück treffen, schmilzt und verdampft das Material. Nach der Entladung entsteht zunächst eine Vakuumblase, welche anschließend zusammenfällt und das geschmolzene Material aus seinem Gefüge löst. Durch die als Funken sichtbaren Entladungen schneidet die Drahtelektrode eine sehr präzise Form in das Werkstück.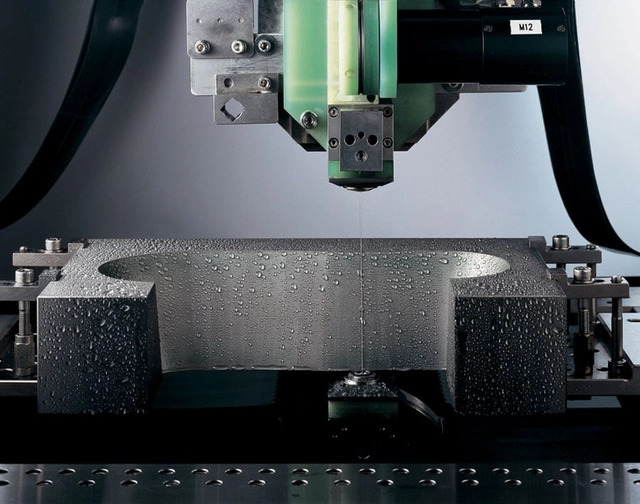
Dank elektrischer Entladung kann ein dünner Draht sogar solche dicken Werkstücke bearbeiten.
PR
Normalerweise würde der dünne Draht durch die Hitze zerstört. Da er sich in einer Flüssigkeit befindet und ständig weiterläuft – mit einer Geschwindigkeit von bis zu 300 Millimetern pro Sekunde –, verbrennt er jedoch nicht. Diese Flüssigkeit ist wenig leitend und wird Dielektrikum genannt; meist handelt es sich dabei um deionisiertes Wasser; auch ein Spezialöl findet hier Verwendung. Die Flüssigkeit muss bei jedem Durchgang aufwändig gekühlt und gefiltert werden, da schon die kleinste Verunreinigung eine saubere und exakte Schnittfläche verhindern kann. Durch die ständige Spülung wird der Draht gekühlt und das verdampfte Material, also der Erodierabfall, aus dem Schnittspalt gespült, während sich der Draht gleichmäßig vorwärtsbewegt. Der Schneidvorgang und die Werkstückbewegung werden von einem Computer gesteuert, welcher vergleichsweise schnell auf die Herstellung anderer Kleinteile programmiert werden kann. Wichtig ist, dass die dem Erodieren vorangegangenen Fertigungsschritte genau mit der Position der erodierten Kontur übereinstimmen, da bereits vor dem Erodieren im Teil befindlichen Bohrungen und Fräsungen am Ende meist im funktionellen Zusammenspiel mit den erodierten Geometrien stehen.
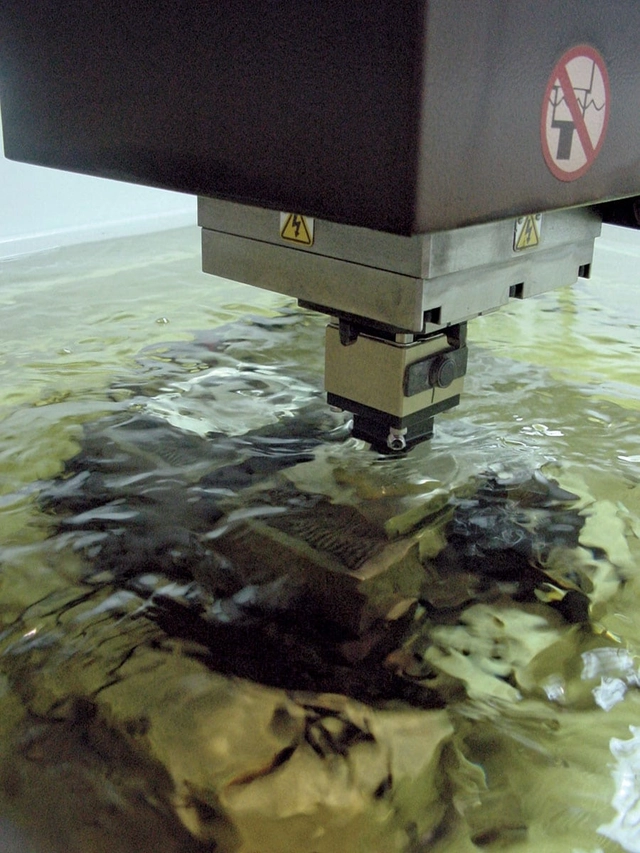
Neben dem Drahterodieren, welches Formen ausschneidet, existiert auch das Senkerodieren, bei welchem Werkstücke von oben bearbeitet werden können.
PR
Von großer Bedeutung bei der Drahterosion ist daher die Produktionsüberwachung, für welche modernste Mess- und Prüfmittel zur Verfügung stehen, zum Beispiel digitalisierte Messverfahren auf einer Drei-Koordinaten-Messmaschine oder auch der traditionelle Profilprojektor. Dabei werden die Konstruktionsvorgaben mit den erodierten Konturen und den Bohrungen und Fräsungen, die sich schon vorher in dem Werkteil befanden, verglichen, um eine Genauigkeit auf den tausendstel Millimeter zu garantieren.
Durch Drahterosion kann jedes elektrisch leitende Material geschnitten werden
Die Drahterosion bietet die geforderte hohe Genauigkeit sowie Oberflächengüte. Ein Vorteil der Drahterosion ist, dass egal, wie hart ein Material ist, jede denkbare Form aus jedem Material gefertig werden kann, solange es elektrisch leitend ist. Jede Verbesserung in der Konstruktion einzelner Werkstücke lässt sich außerdem sofort umsetzen, weil dafür lediglich die Maschine neu programmiert werden muss.
Das Drahterodieren als Verfahren arbeitet allerdings so langsam, dass es sich nicht für hohe Stückzahlen eignet. Allein für das Erodieren der kleinen Zehnerplättchen für die Langematik Perpetual aus Stahlplättchen benötigt die Maschine mehr als zwei Stunden. Alle gefertigten Teile bei A. Lange & Söhne werden aufwändig nachbearbeitet. Ganz in der Tradition des Hauses werden die Oberfläche geschliffen, alle Kanten angliert und das Werkstück gegebenenfalls noch zusätzlich dekoriert.
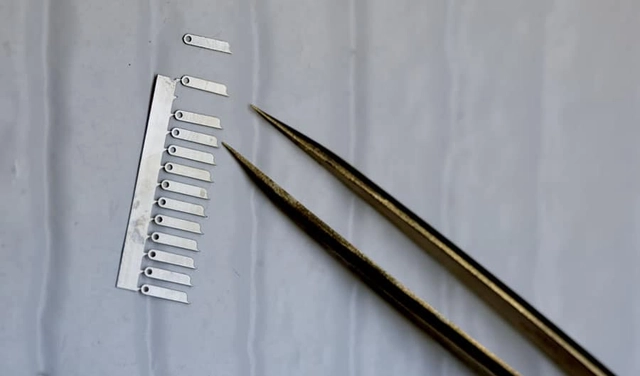
Kleinserie: Typische Uhrwerkteile, wie sie mittels Drahterosion gefertigt werden. Oft liegen mehrere solcher Platinen übereinander.
PR
Die Drahterosion ist eine relativ junge Technologie. Zwar entdeckte der englische Wissenschaftler Priestley die erodierende Wirkung elektrischer Entladungen schon 1770, doch erst in den 1940er-Jahren kamen die sowjetischen Wissenschaftler B. R. und N. I. Lazarenko auf die Idee, die Wirkung elektrischer Entladung nutzbar zu machen. 1943 entwickelten sie ein Bearbeitungsverfahren mit Funkenerosion. Das damals angewandte Prinzip des Entladungsgenerators mit der Bezeichnung Lazarenko-Kreis kam lange Zeit beim Bau von Generatoren für Funkenerosionsmaschinen zum Einsatz. Pioniere auf dem Weg, das Verfahren für die Industrie nutzbar zu machen, waren die AG für industrielle Elektronik, kurz AGIE, aus Losone im Schweizer Tessin, die 1954 die erste Funkenerosionsmaschine präsentierte, sowie die Firma Charmilles aus Genf. 2007 fusionierten die beiden Unternehmen zur Firma GF Agie Charmilles mit Hauptsitz in Meyrin bei Genf, Werken in Losone und Biel sowie der deutschen Vertriebsgesellschaft in Schorndorf bei Stuttgart. Das Unternehmen bietet Maschinen zur Drahterosion sowie Bearbeitungszentren und Automaten. Zum Kundenkreis gehören auch die Schweizer Branchengrößen der Uhrenindustrie, die technische Funktionsteile für das Uhrwerk mittels Drahterosion herstellen. Denn die Vorteile des Schneidens mit Hitze und Funken sind mittlerweile in der zeitgenössischen Uhrenproduktion unverzichtbar.
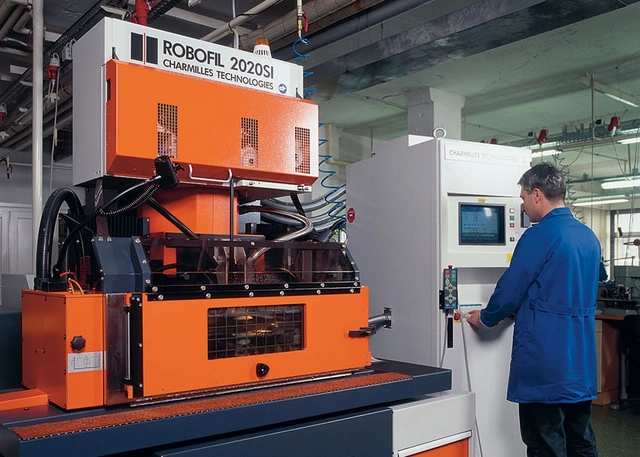
Modernste Technologie aus dem Haus Agie Charmilles: eine Maschine zur Drahterosion.
PR