Zeiger sind die Protagonisten auf dem Zifferblatt: Sie machen die Zeit sichtbar und sind äußerst vielseitig – von klassisch schlicht oder gebläut bis hin zu sportlich und kräftig mit Leuchtmasse ausgelegt. Dementsprechend gibt es in der Herstellung von Zeigern Unterschiede. Der folgende Artikel aus dem UHREN-MAGAZIN Extra Wissen 2015 zeigt, von welchen Unternehmen und auf welche Weise Zeiger gefertigt werden und was hochwertige Zeiger ausmacht.

Klassiker: Die Form der Breguet-Zeiger stammt aus dem 18. Jahrhundert.
PR
Als die Uhr erfunden wurde, war Zeit noch relativ: Die ersten Uhren aus dem 16. Jahrhundert waren mit nur einem Zeiger ausgestattet, der lediglich Auskunft über die aktuelle Stunde gab. Das genügte. Erst Ende des 17. Jahrhunderts ging es genauer zu, als die ersten Uhren mit Minutenzeiger aufkamen. Wie all die anderen Komponenten von Werk und Habillement wurden sie in alten Zeiten selbstverständlich von Hand gefertigt, was sehr aufwändig sein konnte. Bis zu zwei Tagen war der Handwerker mit der Herstellung der Zeiger beschäftigt: Sie wurden von Hand aus Goldblech ausgestochen oder mit Schlag und Hammer aus einem Metallband geschlagen. Ab 1800 konnte man sie durch Stanzen fertigen.
Wer fertigt Zeiger?
Die Herstellung von Zeigern erfolgt heute durch spezialisierte Unternehmen. In der Schweiz ist der Kreis der Zulieferer übersichtlich. Während es zu Beginn des 19. Jahrhunderts noch etwa sechzig Zeigerhersteller gab, sind es heute nur noch ein halbes Dutzend – alle traditionell angesiedelt in den wichtigsten Regionen der Uhrmacherei. Universo, der größte und bekannteste Zeigerhersteller und der Swatch Group zugehörig, hat seinen Sitz in La Chaux-de-Fonds. Beliefert werden die Marken der Swatch Group sowie Drittfirmen. Das Unternehmen mit heute rund 350 Angestellten entsteht 1909 durch die Fusion einer Gruppe kleiner Zeigerhersteller. Außerdem gibt es die Firmen Fiedler (Genf), Waeber (Fleurier), Estima (Grenchen) sowie Aiguilla (Biel). Um ihr Fachwissen zu erhalten und sich gegenseitig zu unterstützen, haben die Fabriken die GFSAH gegründet, das »Groupement des fabricants suisses d’aiguilles pour l’horlogerie« mit Sitz in Neuchâtel. In Deutschland gibt es ebenfalls nur noch wenige Zeigerhersteller; sie fertigen überwiegend Zeiger für Großuhren. Die Firma UTM Uhrenteile-Manufaktur in Schramberg ist hingegen auf Zeiger für Armbanduhren spezialisiert. Das ist jedoch nicht mehr der einzige Geschäftszweig, da seit einigen Jahren die Konkurrenz aus Fernost übermächtig ist. So besitzt der große und bekannte Uhren- und Uhrwerkehersteller Citizen ein eigenes Werk zur Zeigerherstellung, angesiedelt in Tohoku im Norden Japans, rund 500 Kilometer von Tokio entfernt. Zum Angebot gehören sowohl günstige Arbeitszeiger, die bei der Kontrolle von Uhrwerken zum Einsatz kommen, als auch exklusive Zeiger, welche auch in hochwertigen Uhren ihren Platz finden, die ihrerseits weit über hunderttausend Franken kosten.
Das Auftragen von Leuchtfarbe auf die Zeiger kann Handarbeit sein.
PR
Aus dem Ausland kommt heute daher so gute Qualität zu so günstigen Preisen, dass der deutsche Hersteller nicht mehr mithalten kann. Den Schweizer Kollegen ergehe es nicht anders, weiß UTM-Firmeninhaber Ralph-Peter Mannke zu berichten. Er hat bereits Konsequenzen gezogen: Sein Unternehmen konzentriert sich nun auf die Herstellung von hochwertigen Zeigern und offeriert andere Arbeiten rund um die Uhr, zum Beispiel das Lackieren und Bedrucken von Zifferblättern sowie Werkeveredelung und -reparatur. Die größte Erfahrung besitzt man aber nach wie vor bei der Herstellung von Uhrzeigern. Diese wurde in den vergangenen Jahren bei UTM stark automatisiert. Gearbeitet wird mit den modernsten technischen Verfahren. Häufigste Ausgangsmaterialien sind Messing und Neusilber. Bei hochwertigen Uhren dominieren gebläuter Stahl, Platin und Gold.
Aus welchen Materialien werden Zeiger hergestellt?
Bei Quarzuhren mit nicht allzu kräftigem Schrittschaltmotor sowie bei preiswerten Uhren kommt das leichte Aluminium zum Einsatz. Das Metall wird als 0,10 bis 0,15 Millimeter dickes Metallband angeliefert und an besonderen Maschinen weiterverarbeitet. "Viele davon sind Eigenentwicklungen", erklärt Ralph-Peter Mannke von UTM. Auch das Werkzeug wird im eigenen Haus gefertigt – eine schwierige und anspruchsvolle Tätigkeit wegen der kleinen Dimensionen der Zeiger.
In Reih und Glied: Zeigerrohlinge warten auf die Weiterverarbeitung.
PR
Die Metallbänder, aus denen die Zeiger gefertigt werden, bestehen beim Zeigerhersteller Citizen aus Messing, Aluminium und dem so genannten »CuBe« beziehungsweise Cupro-Beyllium, einer sehr harten und teuren Kupfer-Legierung. Diese wird für Chronographenzeiger benutzt, die hohen Kräften ausgesetzt sind, wenn die Rückstellung auf null erfolgt. Aluminium kommt wegen seiner Leichtigkeit überwiegend bei Quarzuhren zum Einsatz. Andere Zeigerhersteller verarbeiten auch Neusilber, gebläuten Stahl, Platin und Gold.
UTM versieht ihre Metallbänder mit seitlichen Führungslöchern, die Transport und Positionierung in den Maschinen mit höchster Präzision ermöglichen. So durchläuft das Band zunächst eine Maschine, welche die Zwischenräume ausstanzt, sodass die Form der Zeiger erhalten bleiben. Jede Zeigerform bedarf ihrer eigenen Werkzeuge, die so mancher Hersteller im eigenen Hause fertigt. Der Stanzvorgang ist so präzise, die Kanten sind so klar definiert, dass einfache Zeiger anschließend ohne weitere Bearbeitung eingefärbt werden können.
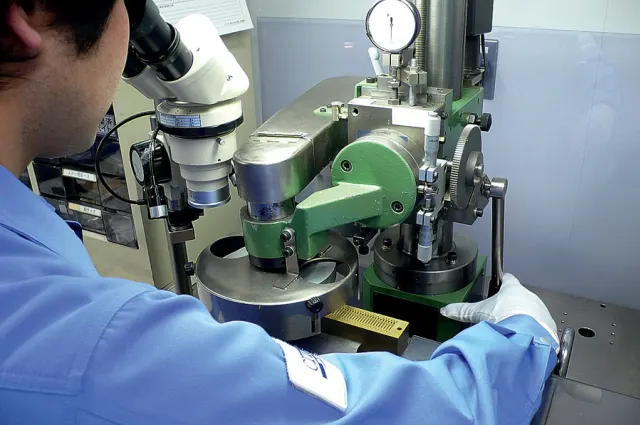
Durch das Diamantieren erhalten die Zeiger eine hochglänzende Oberfläche und einen neuen Querschnitt.
PR
Bei Stunden- und Minutenzeigern wird nach dem Stanzvorgang aus dem Zentrum ihres Kopfes durch Ziehen das Loch verformt, sodass das sogenannte Futter oder die Buchsung entsteht. Dies ist quasi ein Führungsrohr, das später auf das Stunden- beziehungsweise Minutenrohr gedrückt wird und gewährleistet, dass der Zeiger exakt in einer parallel zum Zifferblatt liegenden Ebene rotieren kann. Bei den kleineren Sekundenzeigern wird in einem der letzten Arbeitsgänge die Buchsung von Hand aufgelegt und aufgenietet. Nur bei sehr hochwertigen Stunden- und Minutenzeigern wird das Führungsrohr ebenfalls separat eingesetzt. Nach dem Stanzen, wenn sich die Zeiger noch im Metallband befinden, wird lackiert – ebenfalls ein komplizierter Arbeitsschritt, der Erfahrung bedarf. Dabei legt sich der Lack auch in das Futter der Stunden- und Minutenzeiger. Dieses muss anschließend wieder ausgebohrt werden, um die Toleranzen von sechs Tausendstel Millimetern einzuhalten. Überhaupt ist Genauigkeit oberstes Gebot, deshalb wird nach fast allen Arbeitsgängen nachgemessen. Nach dem Lackieren werden die Zeiger an einer Maschine von Hand einzeln ausgeschnitten, bevor sie galvanisch vergoldet oder vernickelt werden.
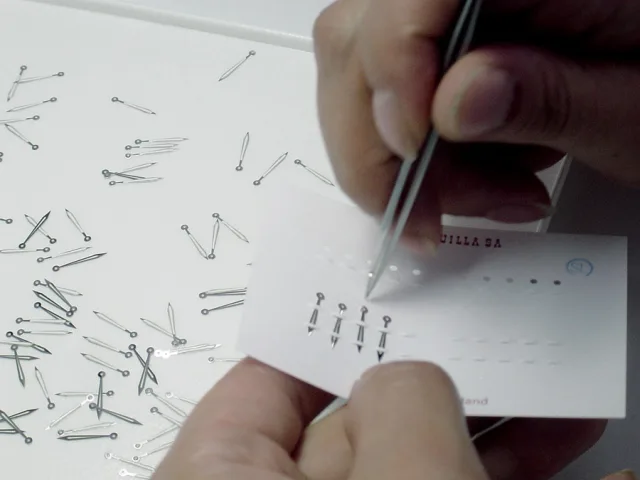
Fertig zum Versand: Die fertigen zeiger des Schweizer Herstellers Aguilla werden auf eine Unterlage gesteckt.
PR
Citizen bietet bei Zeigern hochwertiger Uhren auch das Diamantieren an. Bei dieser Oberflächenbearbeitung mit einem schnellrotierenden, diamantbesetzten Werkzeug wird eine hochglänzende Schnittfläche erzeugt. Dazu werden die Zeigerrohlinge von Hand auf eine entsprechende Befestigung geklebt und danach Stück für Stück von Hand abgenommen und gewaschen. Durch das Diamantieren können Zeiger nicht nur eine hochglänzende Oberfläche, sondern auch einen neuen Querschnitt erhalten: gewölbt oder kantig gefaltet. Diese dreidimensionale Form erhält man auch durch Verformen: Einzeln und von Hand ganz exakt in eine Presse eingelegt, erhalten sie dekorative Wölbungen, Falten oder Kanten. Je nach Modell folgen nun das Hochglanzpolieren, Bläuen oder von Hand das Belegen mit Superluminova, bevor die Zeiger bereit sind zum Einsatz auf dem Zifferblatt.
Die Herstellung von Zeigern für Großuhren erfolgt durch die gleichen Arbeitsgänge, also ebenfalls durch Stanzen mit entsprechenden Nachbearbeitungen; zusätzlich kann CNC-Technik zum Einsatz kommen. Damit umgeht man die teure und aufwändige Herstellung der für jede Zeigerform erforderlichen Werkzeuge; stattdessen wird in Automaten gefräst, gelasert oder durch Wasserstrahl ausgeschnitten.
Woran erkennt man hochwertige Zeiger?
Besonders hochwertige Zeiger können heute noch genauso wie vor über 200 Jahren von Hand aus Goldblech ausgestochen werden, in das die Zeigerumrisse zuvor eingeprägt werden. Der Rohling wird dann mit Siegellack auf einem drehbaren Teller fixiert und von Hand bearbeitet. Dabei ist die geübte Koordination beider Hände gefordert – die linke dreht den Teller, die rechte führt den Stichel. Auf diese Weise werden die nicht durchbrochenen Verzierungen graviert und die Außenkonturen nachgearbeitet. Diese Arbeiten werden unter dem Mikroskop durchgeführt, damit der Stichel genau angesetzt werden kann. Schritt für Schritt werden die Konturen des Zeigers vertieft und anschließend entgratet; die Ornamente werden geglättet, die Unterseite wird geschliffen und das gedrehte, polierte Zeigerfutter aufgepresst. Solch großer Aufwand – die Fertigung eines einzelnen Zeigers dauert zwei bis zweieinhalb Stunden – hat seinen Grund: Die Wertigkeit des Werkes einer Luxusuhr soll schließlich auch auf dem Zifferblatt sichtbar sein.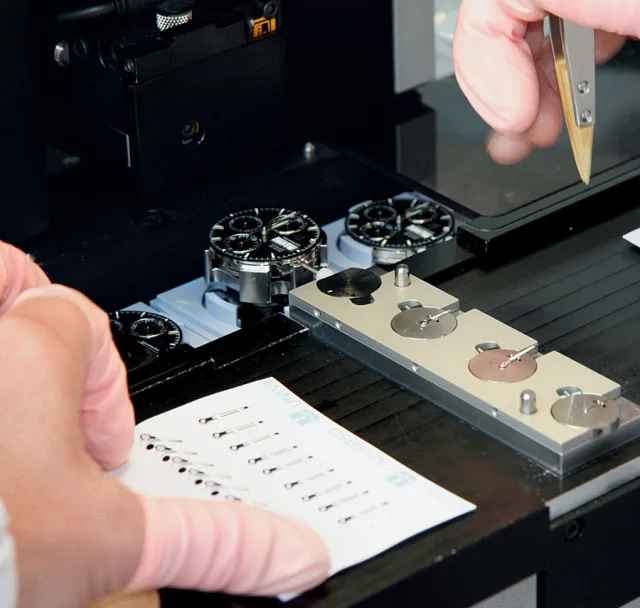
In den Manufakturen der Uhrenhersteller werden die angelieferten Zeiger schließlich auf die Zifferblätter aufgesetzt.
PR
Sind Zeiger hingegen ausschließlich industriell und ohne manuelle Nachbearbeitung hergestellt, entlarvt sich dies meist bei einem genauen, prüfenden Blick: Das Material kann ein offensichtlich dünnes Blech sein, harte Kanten oder eine schlichte Oberfläche besitzen. Es lohnt sich, darauf zu achten. Denn die Zeiger sind ein Detail, das viel zur Ausstrahlung einer Uhr beiträgt.