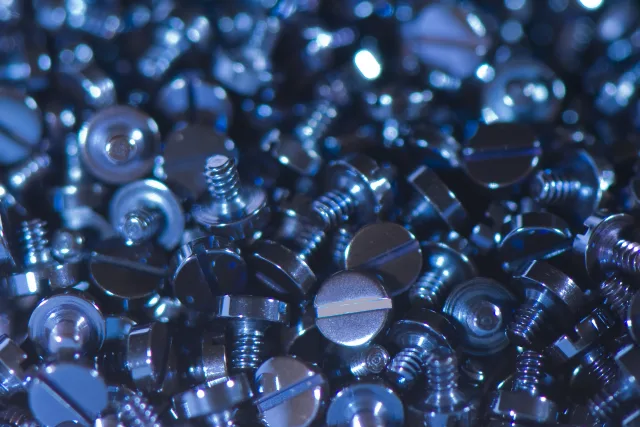
Für eine dunkelblaue Färbung müssen Schrauben zwischen neun und 13 Minuten erhitzt werden
PR
In mechanische Uhrwerke werden gern gebläute Schrauben eingesetzt. Doch auch Zeiger, Federn und andere Stahlteile werden mittels kontrollierter Oxidation auf blauen Kurs gebracht.
Für manchen Liebhaber hochwertiger Zeitmesser sind gebläute Schrauben ein absolutes Muss. Doch mit welcher Technik kommt es zu der schönen blauen Farbe? Manufakturen wie Jaeger-LeCoultre, die große Mengen von Schrauben benötigen, verwenden zum Bläuen einen elektrisch beheizten, mit einigen Umdrehungen pro Minute rotierenden, geneigten Bläuungsofen. Seine Temperatur wird sehr genau geregelt, in seinem Zentrum befindet sich ein nach außen offenes Keramikrohr von ungefähr fünf Zentimetern Durchmesser.
Man heizt auf die gewünschte Temperatur, für Dunkelblau beträgt sie 290 Grad Celsius. Dann bringt man mit einem Stahlschiffchen jeweils einige Tausend Schrauben, die lediglich ein Volumen von einigen Kubikzentimetern einnehmen, in den Boden des Rohrs. Dank der langsamen Drehung des Ofens bleiben die lose geschütteten Schrauben ständig in Bewegung und werden gleichmäßig dem Luftsauerstoff ausgesetzt, ohne dass sie beschädigt werden. Es entsteht ein homogener, farbloser und einige Hundert Nanometer dünner Oxidfilm. Er besteht aus Hammerschlag (Fe3O4, Fe(II), Fe(III) Oxid), der sogenannte Anlass- oder Interferenzfarben entstehen lässt. Dasselbe Phänomen beobachtet man bei Seifenblasen und schwimmenden Ölfilmen, bedingt durch Interferenz des an der Oberfläche des Films beziehungsweise an seiner Rückseite reflektierten Lichts. Wenn die Dicke des Films genau der Hälfte einer bestimmten Lichtwellenlänge entspricht, löschen sich die beiden reflektierten Wellen für diese spezifische Farbe aus. Der verbleibende reflektierte Rest des Sonnen- oder Kunstlichts erscheint dann farbig. Die Wellenlänge des sichtbaren Lichts reicht von 750 Nanometer (rot) bis 400 Nanometer (violett). Je nach Stärke des Films erhält man jeweils eine andere Farbe. Ein dünner Film erscheint gelb, da das kurzwellige blaue Licht ausgelöscht wird. Ein dickerer Film wirkt blau, weil das langwellige Licht der destruktiven Interferenz unterliegt.
In dem ständig auf genau 290 Grad Celsius gehaltenen Bläuungsofen werden die Schrauben zuerst gelblich. Bei wachsender Oxidationszeit wechselt ihre Farbe zu Strohgelb, Goldgelb, Bräunlich, Rot, Purpur und Violett - schließlich erscheint das in der Regel gewünschte Dunkelblau. In diesem Fall ist der Oxidfilm so dick, dass die langwelligen gelb-roten Komponenten des Spektrums um 700 Nanometer ausgelöscht werden. Erhitzt man noch länger, so führt die Oxidation zu Farben höherer Ordnung wie Kornblumenblau, Hellblau und schließlich Dunkelgrau.
Die Dauer der Wärmebehandlung ist sehr kritisch und kann innerhalb weniger Stunden erheblich variieren. Für Dunkelblau sind es je nach Schraubengröße und Toleranz des Thermostaten zwischen 9 und 13 Minuten. Bei der ersten Charge am Morgen muss der Bläuungsprozess von einer perfekt farbkompetenten Person ständig beobachtet werden. So wird die für den Tag richtige Zeit bestimmt und ein Alarm eingestellt. Gegen Ende der eingestellten Zeit muss immer wieder kontrolliert werden. Nur so gelingt es, die exakte Konstanz des Farbtons von Charge zu Charge zu gewährleisten.
Im Ofen korrekt dunkelblau gewordene Schrauben - maßgebend sind Kopf und Schlitz - werden in ein mit Mineralöl gefülltes Emailgefäß abgeschreckt, was die Oxidation schlagartig stoppt. So verfährt auch die Glashütter Marke Nomos. „Das Prinzip der Temperaturbläuung ist Ausdruck von Tradition, und wir betrachten es als hochwertiges, dekoratives Element", berichtet Sylke Schmidt-May, zuständig für Öffentlichkeitsarbeit, und ergänzt: „In unseren Augen ist die traditionelle Methode hochwertiger, weil das Bläuen mit Hitze bestimmtem Kriterien unterworfen ist: Fettrückstände, Unsauberkeiten, aber auch die Luftfeuchtigkeit haben großen Einfluss auf das Ergebnis."
Einzelkämpfer wie die Mitglieder der AHCI (Akademie selbstständiger, schöpferisch tätiger Uhrmacher), die kleine Mengen von Schrauben und anderen Stahlteilen für ihre Uhrwerke selbst bläuen, gehen ganz anders vor. Am einfachsten ist es, die Schrauben mit dem Kopf nach oben in Messingspäne zu stecken und das ganze mit einer Gasflamme zu erhitzen, bis der gewünschte Blauton erreicht ist. Der Farbton muss bei diesem Verfahren nicht bei jedem Los exakt gleich ausfallen. Der Schraubenschaft kann bei diesem Prozess eine andere Farbe annehmen, was nicht unbedingt auffallen muss.
Eine sehr gute Kontrolle des Farbtons erzielt man mit dem bei 300 Grad Celsius schmelzenden Bläuungssalz, einem oxidierenden Gemisch aus Kaliumnitrit und Natriumnitrat mit Spuren von Natriumchlorid, Kaliumchlorid und Natriumbromid. Das Salz wird auf einem Gasrechaud in einem Emailgefäß geschmolzen. Die zu bläuenden Stahlteile werden in diese Salzschmelze gegeben und mit dem gebogenen Ende einer blank polierten Stahlfeder sanft bewegt. Der Fortschritt des Bläuungsprozesses lässt sich auf der Feder viel besser verfolgen als auf den winzigen Schrauben. Sobald der gewünschte Farbton erreicht ist, gießt man die Salzschmelze ab und fängt die Schrauben in einem Teesieb auf, wo sie mit viel Wasser gewaschen und anschließend getrocknet werden.
Die Möglichkeit des chemischen Bläuens steht bei den Herstellern weniger hoch im Kurs. Die Schrauben werden eingekauft und sind üblicherweise mit einem Nickelüberzug versehen, der nur vom Kopf, aber nicht vom Schraubenschlitz, wieder entfernt wird. Die Schraube wird in Bläuungssalz getaucht. Dabei nimmt nur die Oberseite die blaue Farbe an, der Schraubenschlitz mit restlichem Nickelüberzug jedoch nicht.
Die Großuhrenmanufaktur Erwin Sattler in Gräfelfing bevorzugt zwar auch das höherwertige thermische Bläuen, erlaubt jedoch eine Ausnahme: „Wir verwenden Bläuungssalz in erster Linie für größere Mengen Standard-Schrauben. Alle ‚schönen', also verkuppte, angefaste oder polierte Schrauben werden auf einem Lochblech über der Gasflamme gebläut", erklärt Uhrmachermeister Jürgen Kohler. „Bei Zeigern verwenden wir ausschließlich die herkömmliche Methode über der Gasflamme, allerdings in verschiedenen Varianten, mit Spänen- oder ohne auf gebogener Platte", so Kohler weiter.
Dass die im Uhrwerk eingesetzten Stahlteile durch Bläuen vor Rost geschützt werden, gehört zu den Ammenmärchen. Gebläute Schrauben und Federn rosten genau so schnell wie blanke. Im Gegensatz zu den Oxidfilmen auf Aluminium, Titan oder Edelstahl sind Eisenoxidfilme mikroporös und haben so gut wie keine Schutzwirkung. Sauerstoff und Wasserdampf können durch die Oxidschicht hindurch zum Eisen vordringen und Rost verursachen. Einen gewissen Korrosionsschutz bietet hingegen das „schwarz" genannte Polieren: Spiegelglatte Oberflächen mit minimaler Rauheit bieten Korrosion wenig Angriffsfläche.
Text: Lucien F. Trueb, Fotos: Eveline Perroud