Es schien der Anfang vom Ende des Tourbillons. Auf der Baselworld 2004 wurden so viele neue Varianten des Drehgestells gezeigt wie nie zuvor. Jetzt gab es auf dem Markt schon über 100 verschiedene Uhrenmodelle; um die einstmalige Exklusivität dieser Komplikation war es geschehen. Noch schlimmer: Selbst Uhrenmarken, die bislang nichts mit der hohen Uhrmacherkunst zu tun gehabt hatten, boten auf einmal Tourbillons an – oder planten, dies in absehbarer Zeit zu tun. Das Tourbillon drohte vom begehrten Objekt für Kenner zum Spielzeug für Superreiche zu werden. Viele Uhrenenthusiasten machten sich sogar über das neue „Massenprodukt“ lustig.
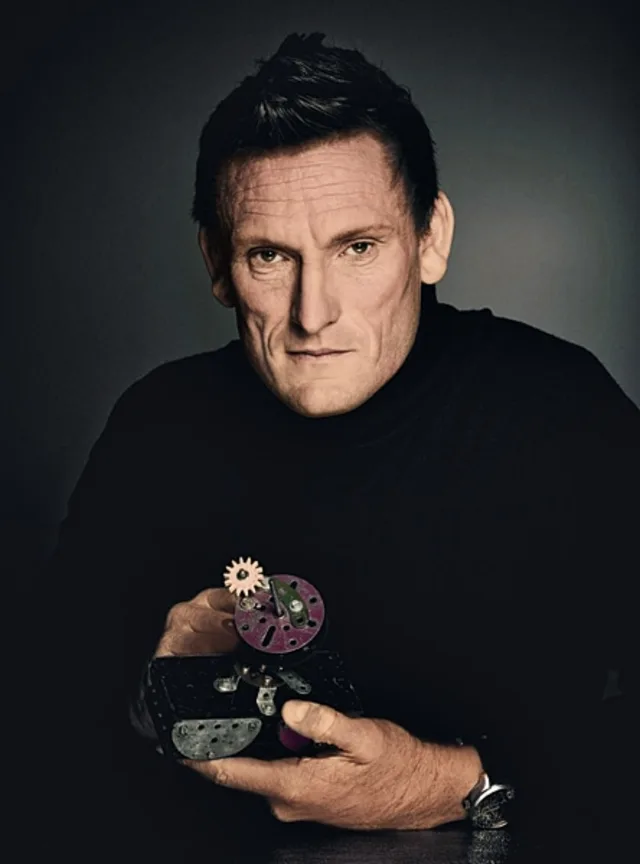
Stephen Forsey mit einem Modell des Double Tourbillon 30°
PR
In einer stillen, wenig frequentierten Ecke der riesigen Messehalle standen auch die beiden Uhrmacher Stephen Forsey und Robert Greubel und präsentierten in ihrer einzigen Vitrine ein brandneues, 380.000 Schweizer Franken teures Tourbillon, das erste Modell ihrer kurz zuvor gegründeten Uhrenmarke Greubel Forsey. „Damals herrschte auf der Messe eine geradezu tourbillonfeindliche Stimmung“, erinnert sich Forsey. Die Leute beklagten sich darüber, dass sich inzwischen jeder eines fertigen lassen könne, daher sei, so die allgemeine Stimmung, „das Thema durch“.
Doch Greubel und Forsey ließen sich nicht unterkriegen. Sie hatten auch keine andere Wahl, denn schließlich hatten sie fast fünf Jahre lang an ihrer Uhr gearbeitet und jeden Cent in die fünf Musterexemplare gesteckt, die sie nach Basel gebracht hatten. „Wir mussten einfach Kunden dafür finden“, so Forsey. Glücklicherweise – und aller Wahrscheinlichkeit zum Trotz – gelang ihnen dies auch. Kunden und Journalisten waren gleichermaßen von dem kleinen „Wirbelwind“ beeindruckt, der so völlig anders war als alle bislang gesehenen. Es handelte sich um ein Doppeltourbillon, das sich in verschiedenen Geschwindigkeiten um zwei Achsen dreht und bei dem das innere Drehgestell in einem Winkel von 30 Grad zum äußeren gelagert ist. Sie nannten die Uhr ganz einfach „Double Tourbillon 30°“. Die Käufer kauften, und die Journalisten kritzelten in ihre Notizblöcke, was das Zeug hielt.

Robert Greubel
PR
Daran hat sich bis heute nichts geändert. Die in La Chaux-de-Fonds ansässige Uhrenmarke hat es zu einer Berühmtheit gebracht, die in keinem Verhältnis zu den rund 100 Uhren steht, die sie pro Jahr fertigt. Ein Grund dafür sind ihre unorthodoxen Werkedesigns, ein anderer die Tatsache, dass sie ausschließlich Tourbillons herstellt und damit die einzige Marke ist, die ihr Repertoire auf diese Weise limitiert. Ein weiterer Grund ist die viel gepriesene Verarbeitungsqualität der Uhrenmarke, insbesondere die sorgfältige und ungewöhnliche Finissierung ihrer Werke. Ganz zu schweigen von ihren Preisen, die bei etwa 225.000 Euro beginnen und damit zu den höchsten in der Uhrenwelt zählen.

Das Doppeltourbillon mit seiner geneigten Unruh
PR
Uhren statt Autos
Wie hat das Duo es so weit gebracht? Chronos traf Forsey, den technischen Leiter des Unternehmens – Greubel konzentriert sich auf das Kreative –, in der neuen Uhrenmanufaktur in La Chaux-de-Fonds, um die Geschichte der Gründer und ihrer Firma zu hören. Für Forsey begann der Weg zum Tourbillon-Ruhm genau damit: mit dem Weg. 1967 geboren, wuchs er im rund 35 Kilometer nördlich von London gelegenen St. Albans auf. Sein Vater war ein Bentley-Liebhaber und verbrachte seine Freizeit mit der Restauration von Oldtimern. Noch während er die Grundschule besuchte, half er seinem Vater bei dessen Hobby, indem er ihm immer den passenden Schraubenschlüssel für den nächsten Handgriff heraussuchte. „Mir hat das von Anfang an Spaß gemacht“, sagt Forsey über seine Tätigkeit als Handwerkergehilfe.
Als er 10 oder 12 Jahre alt war, fachte sein Großvater, ein Ingenieur, Stephens wachsende Begeisterung für alles Technische noch weiter an, indem er ihm die Bedienung einfacher Werkzeugmaschinen beibrachte. Forsey schien für eine Ingenieurslaufbahn bestimmt zu sein, bis ihn eine zufällige Begegnung in eine andere Richtung lenkte. Einer seiner Bekannten, ein Autoliebhaber, der auch ein Faible für Uhren hatte, besaß eine Werkstatt für die Restauration antiker Uhren. „In dieser Werkstatt eröffnete sich mir ein Weg, der die Technik mit einer künstlerischen Tätigkeit verband“, sagt Forsey. Statt Ingenieurswissenschaften zu studieren, wie es seine Eltern und sein Großvater gehofft hatten, beschloss Forsey, gleich mit der Uhrmacherei anzufangen. Mit einigen Schwierigkeiten – es war Mitte der achtziger Jahre, und das Revival der mechanischen Uhr hatte noch nicht stattgefunden – fand er eine Uhrmacherausbildung am Hackney Technical College in London. Nach Abschluss seiner Ausbildung arbeitete er in der Abteilung für Uhrenrestauration des berühmten Luxus-Kaufhauses Asprey in London. Während der fünf Jahre dort war er nicht nur über drei Jahre lang Leiter dieses Bereichs, sondern absolvierte auch zwei Kurse an der Uhrmacherschule WOSTEP in Neuchâtel.

Das Double Tourbillon 30° Vision, eine Variante mit größerer Zifferblattöffnung als das Original, gewährt einen ungehinderten Blick auf die Doppeltourbillons
PR
Es war eine unsichere Zeit für die Uhrmacherkunst, erinnert sich Forsey: „Als ich zur WOSTEP kam, war alle sechs Monate die Rede davon, die Schule zu schließen. Damals gab es nur noch drei solcher Schulen in der Schweiz. Das letzte Wort über den Fortbestand der mechanischen Uhr war noch nicht gesprochen.“ Ermutigt wurde er durch eine kleine Gruppe unerschütterlicher Mechanikliebhaber, die wussten, dass Uhren mit Hand- oder Automatikaufzug eines Tages ihr Comeback feiern würden. Einer von ihnen war George Daniels, der berühmte britische Uhrmacher, den Forsey 1986 über seinen Vater kennen gelernt hatte. Daniels bestärkte ihn durch seine Fähigkeit, eine Uhr im Wesentlichen von A bis Z zu fertigen. „Er zeigte mir, dass ein Einzelner sämtliche Arbeitsschritte für die Fertigung einer mechanischen Uhr beherrschen kann“, sagt Forsey.
1992 beendete Forsey seine Mitarbeit bei Asprey und machte sich auf ins Mekka der Zeitmesser, die Schweiz, um seine Träume von einer Uhrmacherkarriere zu verwirklichen. Einer seiner Freunde arbeitete bei dem Werkehersteller Renaud & Papi in Le Locle und arrangierte ein Vorstellungsgespräch. Forsey traf den stellvertretenden Geschäftsführer, einen Franzosen namens Robert Greubel. Dieser war zuvor bei IWC tätig gewesen, wo er an der berühmten Grande Complication gearbeitet hatte. Obwohl Forsey kein Französisch sprach und Greubel nur wenig Englisch, einigten sich die beiden, und Forsey trat dem Unternehmen bei.
Aus Alt mach Neu
Ursprünglich wollte er ein oder zwei Jahre bei Renaud & Papi bleiben. Stattdessen blieb er sieben Jahre, bis 1999: „Anfangs arbeitete ich an der Werkbank und baute Komplikationen – hauptsächlich Minutenrepetitionen. Dann war ich Prototypist und arbeitete an der ersten Grande Sonnerie.“ Im Laufe der Zeit arbeiteten Greubel und Forsey immer enger zusammen, und Forsey lernte auch Französisch. Schließlich wurde er Projektleiter und verantwortlich für die Assemblage-Abteilung, in der komplizierte Werke gefertigt wurden.
Eines Tages unterhielten sich die beiden über ihr Lieblingsthema, Komplikationen, und stellten fest, dass sie praktisch die gleiche Idee hatten: einen bestehenden Mechanismus zu überdenken, zu verbessern und selbst zu fertigen. „Daraufhin beschlossen wir, uns selbstständig zu machen“, erinnert sich Forsey. Ebenso schnell entschieden sie sich für das Tourbillon als ihre Spezialität. Ihrer Meinung nach sprach viel dafür. Zum einen genoss es den Ruf, das Symbol hoher Uhrmacherkunst schlechthin zu sein, denn kein anderer Mechanismus stellt das Können eines Uhrmachers mehr auf die Probe. Zum anderen waren sie davon überzeugt, dass das Tourbillon das Potenzial habe, eine weit wichtigere Rolle zu spielen als zuvor. Sicher war der Einwand der Skeptiker, das einst für Taschenuhren ersonnene Tourbillon sei in Armbanduhren von geringem Nutzen, in gewissem Maße berechtigt. Aber was wäre, wenn sie diesem Einwand ein Tourbillon speziell für Armbanduhren entgegensetzen könnten?

Vorder- und Rückansicht (oben) des ersten Quadruple Tourbillon à Différentiel
PR
Darüber hinaus wussten die beiden, dass seit der Patentierung durch Abraham-Louis Breguet vor über zwei Jahrhunderten nur wenige Versuche zur Verbesserung dieses Bauteils unternommen worden waren. Insgesamt waren es nur drei wirkliche Versuche, betont Forsey. Den einen unternahm im 19. Jahrhundert der amerikanische Uhrmacher Albert Potter, den anderen 1927/28 der Deutsche Walter Prendel. Beide verwendeten eine Unruh, deren Achse gegenüber der des Tourbillons geneigt war. Die dritte Innovation, ein bi-axialer Mechanismus für Reiseuhren, nicht aber für Armbanduhren, präsentierte der Brite Anthony Randall in den 1970er Jahren. Forsey: „Wir waren der Meinung, es sei an der Zeit, dieses Thema weiter zu erforschen.“ Also nahmen die beiden 1999 die Aufgabe in Angriff, ein besseres Tourbillon zu kreieren, denn die gewöhnlichen kannten sie bereits in- und auswendig. „Bei Renaud & Papi hatten wir an zahlreichen traditionellen, einachsigen Armbanduhren-Tourbillons gearbeitet. Wir konnten sie somit eingehend erforschen – sowohl die gut funktionierenden als auch die, die Probleme machten“, erzählt Forsey.
Aber schließlich wollten sie etwas Ungewöhnliches bauen, und dafür brauchten sie Zeit und Geld. Woher aber letzteres bekommen? Die beiden beschlossen, eine Firma in LaChaux-de-Fonds zu gründen, mit der sie durch die Fertigung von komplizierten Uhrwerken das nötige Geld verdienen würden. Währenddessen wollten sie an der Verwirklichung ihres Tourbillon-Traums arbeiten. Sie nannten ihre 2001 gegründete Firma „CompliTime“. „Durch sie fanden wir genug Kunden zum Leben“, so Forsey.
Das Resultat ihrer Entwicklungsarbeit waren schließlich 17 verschiedene Tourbillonmechanismen – Greubel und Forsey nennen sie „grundlegende Erfindungen“. Die ersten beiden verwendeten sie in ihrem Double Tourbillon 30°, das sie unter jenen ungünstigen Umständen auf der Baselworld 2004 präsentierten. Am meisten unterschied sich die Uhr von anderen durch die Tatsache, dass ihr innerer Tourbillonkäfig, der sich einmal pro Minute um die eigene Achse dreht, in einem 30-Grad-Winkel zum äußeren Käfig gelagert ist. Dieser dreht sich wiederum einmal in vier Minuten. Indem sie den inneren Käfig schräg lagerten, beabsichtigten Greubel und Forsey zu beweisen, dass ein Tourbillon tatsächlich die Ganggenauigkeit einer Armbanduhr verbessern könne. Es gleicht Störungen aus, die sich durch die Wirkung der Erdanziehung auf die Unruh ergeben. Die Störungen, die das Tourbillon vor zwei Jahrhunderten ausgleichen sollte, waren die einer Taschenuhr. Ihre normale Position war eine senkrechte, nämlich in einer Westentasche getragen, mit einer nach rechts oder links geneigten Krone. Die Situation bei einer Armbanduhr ist jedoch eine ganz andere, denn sie verändert beim normalen Tragen ständig ihre Lage. Im Gegensatz zu einer Taschenuhr verbringt sie nur einen Bruchteil der Zeit in einer exakt senkrechten Lage.
Forsey und Greubel war klar, dass sie dem Tourbillon eine andere Rolle zuweisen mussten, sollte es in einer Armbanduhr von Nutzen sein. Sie beschlossen, die neue und verbesserte Version zur Vermeidung einer exakt vertikalen oder horizontalen Lage der Unruh zu verwenden. Dies würde die durch Lagenwechsel bedingten Gangunterschiede minimieren und deren Korrektur bei der Regulierung der Uhr erleichtern. „Wenn man die Extreme reduziert, erhält man eher ein besseres Ergebnis“, erläutert Forsey. Das geneigte Tourbillon mit zwei Achsen bewirkt genau dies: Es hält die Unruh ständig so in Bewegung, dass sie sich niemals genau in einer horizontalen oder vertikalen Lage befindet, sondern immer nur in dazwischen liegenden Positionen.
Noch mehr Tourbillons
Laut Forsey bietet der Winkel von 30 Grad noch einen weiteren Vorteil. Er ermöglicht es dem Unternehmen, eine große Unruh zu verwenden, was besser für die Ganggenauigkeit ist. Trotzdem kann die Uhr mit einer Höhe von etwa 16 Millimetern relativ flach gehalten werden. „So konnten wir einen Unruhreif von fast elf Millimetern Durchmesser in ein Werk einbauen, das nur 9,65 Millimeter hoch ist“, sagt er. In zweiachsigen Tourbillons mit Käfigen, die in einem Winkel von 90 Grad zueinander rotieren, muss das Werk hoch genug für den gesamten Durchmesser der Unruh sein“, erklärt Forsey. „Der Unruhreif muss sich um die eigene Achse drehen. Also kann man ihn niemals so bauen, dass sein Durchmesser größer als die Werkhöhe ist.“

In der Manufaktur sind verschiedene Betriebsabläufe vereint, die zuvor in verschiedenen Werkstätten erfolgten
PR
Aufgrund ihrer Kompetenz zog sie sehnsüchtige Blicke der Richemont-Gruppe auf sich, die Greubel und Forsey von ihren früheren Tätigkeiten her kannten. Richemont wollte einen Anteil an CompliTime erwerben, so Forsey, doch er und sein Partner wollten die Firma nicht verkaufen. „Das Fundament von CompliTime ist ihre Unabhängigkeit, und zwar zu 100 Prozent“, erklärt er. Stattdessen verkauften sie der Gruppe einen 20-Prozent-Anteil an Greubel Forsey. Auf diese Weise erlangte der Luxusgütergigant eine Verbindung zu CompliTime, aber keine direkte Kontrolle darüber. Forsey: „Die 20 Prozent an Greubel Forsey waren eine gute Lösung für Richemont, denn so hat Richemont durch Robert und mich eine Verbindung zu CompliTime.“
Auch für Greubel Forsey war es eine gute Lösung. Obwohl die beiden Partner nicht aktiv nach einem Geldgeber gesucht hatten, ermöglichte ihnen die Kapitalspritze von Richemont Investitionen, die sie sonst nicht so schnell hätten realisieren können. Dazu gehört eine neue Manufaktur am Rand von La Chaux-de-Fonds. Sie wurde 2009 eröffnet und vereint Betriebsabläufe, die zuvor in verschiedenen, über ganz La Chaux-de-Fonds verstreuten Werkstätten stattfanden, unter einem Dach. Sie besteht aus zwei Gebäuden, einem unter Denkmalschutz stehenden Bauernhaus aus dem 18. Jahrhundert sowie einem keilförmigen Glasbau ganz im Stil des 21. Jahrhunderts, ausgestattet mit einer Reihe umweltfreundlicher Attribute.
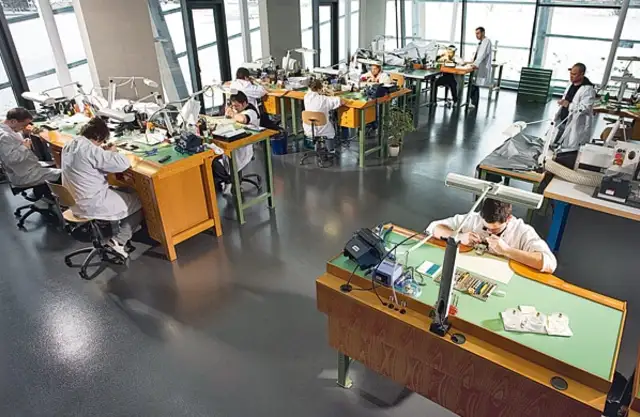
Die Finissage-Abteilung in der neuen Manufaktur
PR

PR
Ort der Extreme
Die Uhrenmanufaktur Greubel Forsey in dem Eplatures genannten Industriegebiet am Rande von La Chaux-de-Fonds hoch in den Bergen des Jura beherbergt Widersprüche und unerwartete Extreme zuhauf: uralt und brandneu, riesig und winzig, langsam wie eine Schnecke und schnell wie ein Blitz.
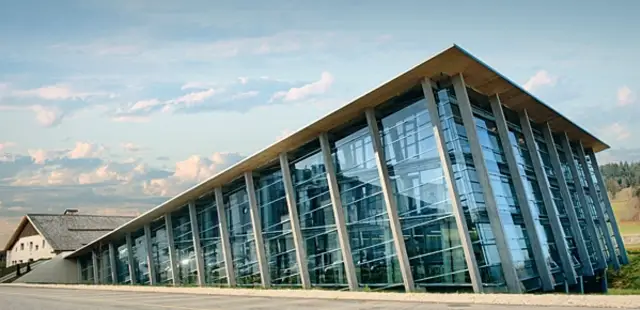
Manufaktur Greubel-Forsey in Eplatures (La Chaux-de-Fonds)
PR
Das Unternehmen eröffnete die Uhrenmanufaktur 2009 und vereinte damit die Fertigungsschritte, die zuvor in acht verschiedenen, über ganz La Chaux-de-Fonds verstreuten Werkstätten erfolgten, unter einem Dach. (Die Schwesterfirma CompliTime teilt sich die Betriebsstätte mit Greubel Forsey und stellt komplizierte Werke für andere Uhrenfirmen her.)
Eines der beiden Gebäude ist ein Bauernhaus, in dem sich Empfangs- und Besprechungsräume befinden. Es wurde im 18. Jahrhundert in dem für den Kanton Neuchâtel typischen Stil erbaut. Ein Torbogen, der sich ursprünglich in einem anderen Gebäude befand, stammt sogar aus dem Jahr 1686. Das ganze Haus verströmt den Zauber vergangener Zeiten, angefangen von seinem rustikalen Weinkeller bis zu seiner Holzbalkendecke.
Begibt man sich in das ans Bauernhaus angebaute Gebäude, taucht man in eine andere Welt ein: in eine hochmoderne, glas-ummantelte Betriebsstätte voller neuer Maschinen. Zur besseren Isolierung besitzt sie zwei Gebäudehüllen und ist mit sämtlichen umweltfreundlichen Attributen ausgestattet, die man sich nur vorstellen kann. Das Frappierendste ist jedoch ihr geringer Ausstoß. In dieser geräumigen Manufaktur mit ihren 2.800 Quadratmetern werden weniger als 200 Stück pro Jahr gefertigt: rund 100 für Greubel Forsey und ein paar Dutzend weitere für CompliTime.
Etwa 100 Mitarbeiter fertigen hier Uhrenteile – 60 bis 70 Prozent der Werkkomponenten von Greubel Forsey werden in der eigenen Manufaktur hergestellt –, setzen sie zusammen und finissieren sie anschließend in der größten Abteilung der Betriebsstätte.
Die CNC-Maschinen der Manufaktur laufen weit unter Kapazität. Normalerweise versuchen Firmen, solch teure Maschinen so gut wie möglich auszulasten. Hier jedoch sind die Fertigungsläufe so kurz, dass sie den größten Teil des Tages programmiert werden. Sie produzieren ein paar Teile, zum Beispiel 30, und halten dann an, um für die nächste Komponente eingestellt zu werden. Sieben CNC-Maschinen, die in den meisten Betrieben von zwei Personen bedient würden, erfordern hier fünf Mitarbeiter. Es kann bis zu einer Woche dauern, um sie für eine Komponente zu programmieren, deren Produktion gerade einmal zehn Minuten erfordert, sagt Stephen Forsey. Und weil die Toleranzen für manche Komponenten so gering sind – in einigen Fällen nicht mehr als ein vier tausendstel Millimeter – kommt die Einstellung von Mitarbeitern, die diese einhalten können, einem Ganztagsjob gleich. „Leute zu finden, die qualifiziert genug für die Bedienung der Maschinen sind, stellt eine größere Herausforderung dar, als die Maschinen zu finanzieren“, erläutert Forsey. Das Unternehmen brauchte drei Jahre, um jemanden mit genügend Fachkompetenz für die Bedienung der anspruchsvolleren zu finden.
Auch die Beschaffung der Materialien für die winzigen Produktionsläufe ist nicht einfach. Metalllieferanten fordern eine Mindestbestellmenge von beispielsweise einer Tonne oder gar noch mehr. Für Greubel Forsey jedoch mögen schon fünf Kilo ausreichend sein. „Wir haben hier wahrscheinlich einen Vorrat für zwei bis drei Jahre“, sagt Forsey und zeigt auf einige Metallteile. „Normalerweise muss man von einem solchen Material eine Tonne kaufen. Das hier jedoch sind wohl kaum mehr als zwei Kilo. Als wir anfangs Material für die Werkplatten kaufen wollten, sagte unser Lieferant, wir müssten fünf Tonnen abnehmen. Selbst wenn wir jeden aus der Manufaktur hinauswerfen würden, hätten wir nicht genug Platz für fünf Tonnen. Das sind unsere Herausforderungen“, sagt er.