Seit 2009 ist Breitling Manufaktur. Im Interview mit Chronos-Chefredakteur Rüdiger Bucher (Interview aus Chronos 4.2012) spricht Breitling-Vizepräsident Jean-Paul Girardin über die Entwicklung des ersten eigenen Kalibers und den Ausbau zu einer Werkefamilie.
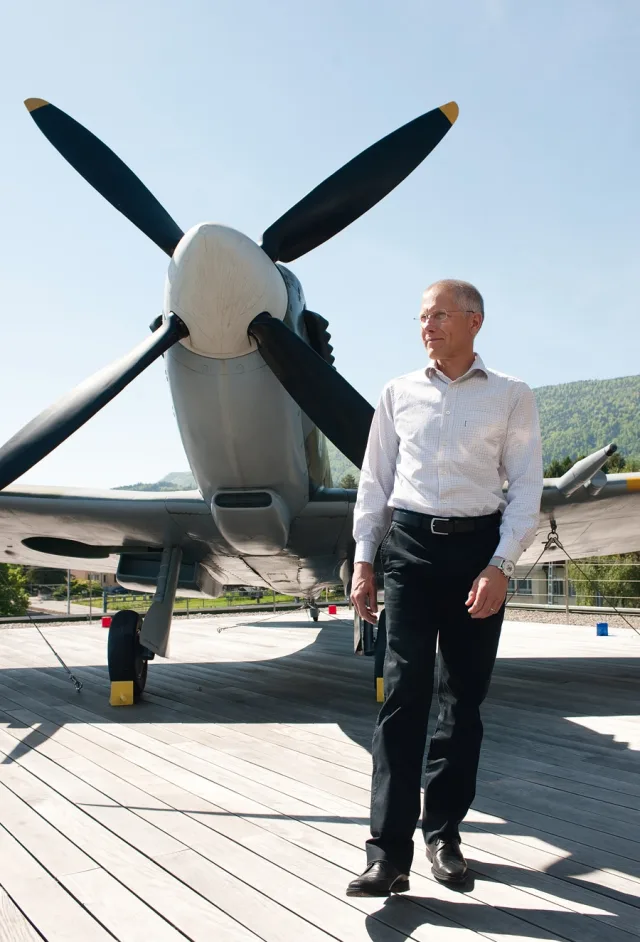
Jean-Paul Girardin
PR
Breitling präsentierte 2009 sein erstes eigenes Werk, das Kaliber 01, ein Chronographenwerk mit Automatikaufzug und Schaltrad. Wann fiel die Entscheidung für die Entwicklung dieses Kalibers, und was ist die Strategie dahinter?
Die Idee gab es schon seit längerem. Sie erinnern sich: Wir hatten 1999 begonnen, alle unsere Werke von der COSC als Chronometer zertifizieren zu lassen. Schon damals stellten wir uns die Frage, was wir als unabhängiges Unternehmen tun müssten, um langfristig unseren Erfolg zu sichern. Es war klar, dass es nicht der richtige Weg sein würde, alles selbst zu machen, denn es gibt für viele Einzelteile erstklassige, hochspezialisierte Lieferanten. Gleichzeitig fragten uns unsere Kunden in Märkten wie Deutschland, der Schweiz und Japan immer häufiger, warum wir als Leader bei mechanischen Chronographen keine eigenen Werke fertigen würden. Das Thema war also schon da. Den konkreten Anlass gab dann die Ankündigung der Eta im Jahr 2002, die Lieferung von Rohwerken nach und nach auslaufen zu lassen.
Die Eta wollte künftig statt Rohwerken nur noch komplette Werke ausliefern und gleichzeitig die Liefermengen reduzieren oder zumindest deckeln. So ist es dann auch geschehen.
Das erste machte die Sache etwas umständlicher für uns, war aber kein großes Problem. Aber auf die Reduzierung mussten wir reagieren. Zumal klar war, dass wir von nun an keinesfalls höhere Stückzahlen würden bestellen können. Dazu kam, dass wir unseren Kunden mittelfristig auch Uhren mit neuen, zusätzlichen Funktionen anbieten wollten. Die Entscheidung, eine eigene Werkefertigung aufzubauen, inklusive einer neuen Abteilung für Forschung und Entwicklung, beruhte also auf einer industriellen Strategie. Sie resultierte nicht aus Marketinggesichtspunkten. Es ging uns nicht darum, etwa eine limitierte Serie mit eigenen Werken herauszubringen, nur um sagen zu können: Wir sind jetzt eine Manufaktur.
Es begann also mit der Einrichtung der Entwicklungsabteilung.
Zunächst brauchten wir ein paar Monate, um zu analysieren, in welche Richtung wir gehen sollten. Sollten wir die bisher bezogenen Werke kopieren? Oder uns einfach nach alternativen Lieferanten umsehen? Letztlich war uns unsere Unabhängigkeit am wichtigsten. So beschlossen wir, künftig unsere eigenen Werke zu fertigen. In Genf fanden wir sehr gute Konstrukteure.
Wann war das, und mit wie vielen Konstrukteuren fingen Sie an?
Das war 2004. Zunächst hatten wir vier Konstrukteure, später fünf. Wir haben sie in einer neuen Gesellschaft mit Sitz in Genf zusammengefasst, unter dem Namen Professional Flight Instruments (PFI).
Warum in Genf?
Zum einen, weil die Konstrukteure aus der Gegend stammten und nicht unbedingt nach Grenchen oder La Chaux-de-Fonds umziehen wollten. Zum anderen der Diskretion wegen.
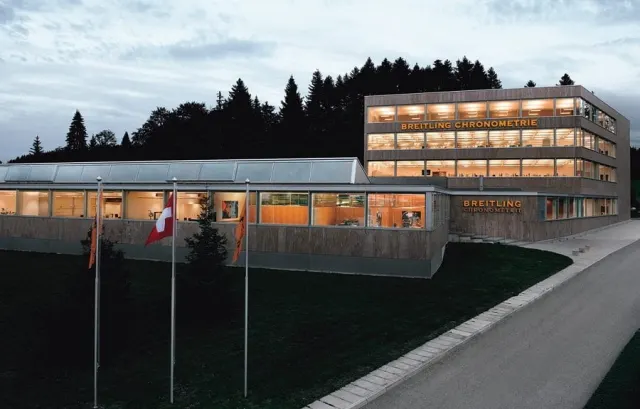
Manufakturgebäude: die Breitling-Chronométrie in La Chaux-de-Fonds
PR
Welche Eigenschaften hatten Sie im Pflichtenheft für Ihren ersten eigenen Chronographen vorgesehen?
Hohe Leistung, Zuverlässigkeit, Ganggenauigkeit – und selbstverständlich sollte er COSC zertifiziert sein. Das Werk sollte flacher sein als das Valjoux 7750, möglichst einen ganzen Millimeter, und sich leicht reparieren lassen. Eine offene Architektur sollte die Kombination mit weiteren Komplikationen ermöglichen. Und nicht zuletzt sollte sich das Werk in den von uns benötigten Stückzahlen produzieren lassen. Das Kaliber sollte also mehr bieten als ein 7750. Es war klar, dass es damit auch teurer sein musste, aber es sollte unter dem Doppelten bleiben.
Wann waren die ersten Prototypen fertig?
Nach zwei Jahren, 2006. Im Sommer haben wir sie getestet. Dabei war uns klar, dass wir höchstens die Hälfte des Weges zurückgelegt hatten. Nun ging es um die Industrialisierung.
Von Industrialisierung wird oft gesprochen. Wie läuft so etwas ab?
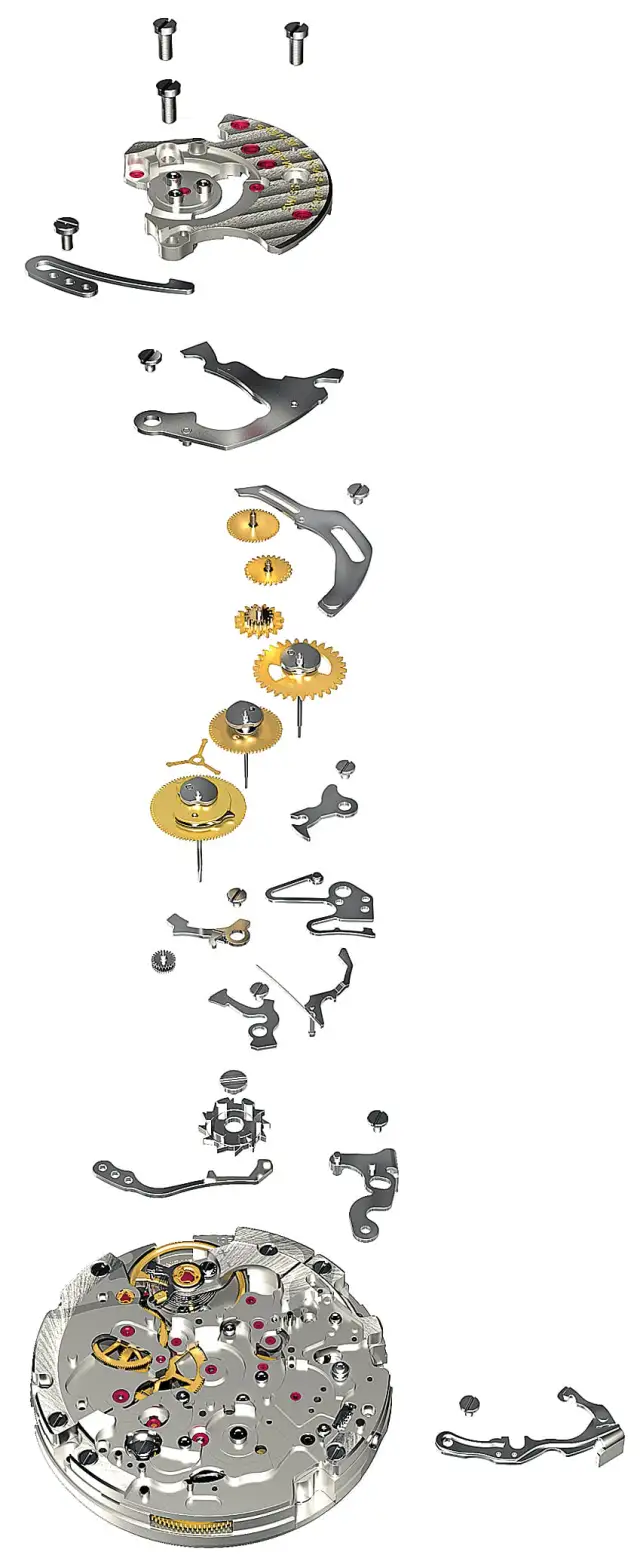
Das erste eigene Werk: Breitlings Chronographenkaliber 01
PR
Nun, letztlich geht es darum, die Konstruktion in die Praxis umzusetzen und dafür zu sorgen, dass man in den geforderten Stückzahlen produzieren kann. Dass man die benötigten Maschinen hat. Dass man eine Qualitätssicherung hat. Und dass man bei den Teilen, die man nicht selbst herstellt, die Belieferung sicherstellt. Wir haben damals entschieden, dass wir strategisch wichtige Teile selbst fertigen sowie Teile, für die wir nicht zwei unabhängige Lieferanten finden können.
Welche Teile sind das?
Zum Beispiel Messingteile wie Brücken, Platinen oder Kalenderscheiben. Was wir auch in-house machen, sind bestimmte Arbeitsschritte in der Vormontage wie das Einpressen der Lagersteine in Brücken und Platinen. Letzteres ist sehr wichtig, weil man dann die Qualität selbst kontrolliert und somit weiß, wie gut die Teile sind, die man hinterher verbaut. Dann gibt es Teile wie die Schalträder, die wir in kleinen Mengen selbst herstellen können, etwa für Prototypen. Wir brauchen aber nicht alle Teile für die Serienproduktion selbst zu fertigen, da es dafür genügend spezialisierte Lieferanten gibt. Das Paradox der Fertigung eigener Werke besteht darin, dass man auf einmal noch viel mehr Lieferanten hat. Dadurch wird auch die Logistik wesentlich komplexer.
Wo fand die Industrialisierung des Kalibers 01 statt?
In der Breitling Chronométrie in La Chaux-de-Fonds. Dort hatten wir zuvor schon die Eta-Rohwerke und die Module von Dubois Dépraz assembliert, die Werke für die COSC reguliert und fertige Werke in die Gehäuse eingeschalt. Für die Produktion unserer eigenen Kaliber haben wir dort kräftig investiert und die Nutzfläche von 2000 auf 6000 Quadratmeter ausgebaut.
Wie viele Leute arbeiten jetzt dort?
Wir haben dort 200 Mitarbeiter, dazu noch einmal 200 in Grenchen sowie die fünf in Genf in unserer Forschungs- und Entwicklungsabteilung, die heute Breitling Technologie heißt.
Die Industrialisierung war dann 2009 abgeschlossen.
Ja. 2009 konnten wir unser erstes eigenes Kaliber, das Breitling 01, auf der Baselworld vorstellen, und zwar in einer Chronomat, unserem Bestseller. Wir haben ganz bewusst nicht eine limitierte Serie von etwa 1000 Stück herausgebracht, um keinen Zweifel daran zu lassen, dass wir große Stückzahlen beherrschen.
Vor kurzem gaben Sie bekannt, dass Sie die Garantie für Uhren mit Ihrem eigenen Kaliber von zwei auf fünf Jahre heraufsetzen.
Wir wissen, dass die Zuverlässigkeit des Werks sehr hoch ist. Und die Erfahrung der ersten drei Jahre hat das bestätigt. Somit können wir unseren Kunden einen weiteren Mehrwert bieten. Sie müssen allerdings alle zwei Jahre einen – kostenlosen – Wasserdichtheits-Check durchführen lassen.
Breitling fertigt zwischen 150.000 und 200.000 Uhren pro Jahr. Wie viele davon mit eigenen Werken?
Die Hälfte unserer Uhren sind Chronographen mit mechanischen Werken. Und davon wiederum sollte die Hälfte mit eigenen Kalibern ausgestattet sein, das war unser Ziel. Die Kapazitäten sind auf 50.000 eigene Werke pro Jahr ausgelegt. 2011 waren es bereits 40.000.
Wenn es jetzt schon 40.000 sind: Reichen dann langfristig 50.000 aus?
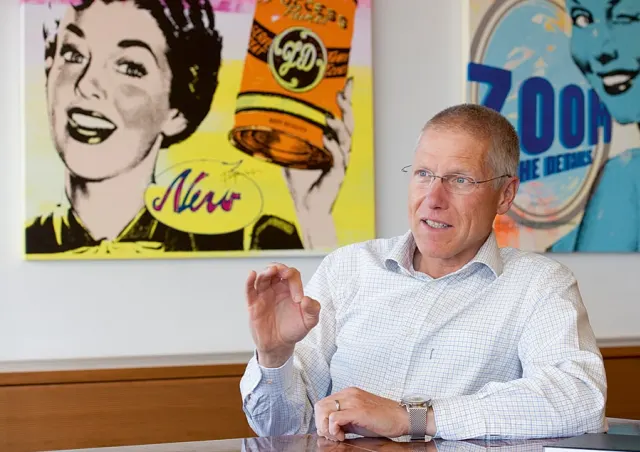
Girardin: „Unsere Kapazitäten sind auf 50000 eigene Werke pro Jahr ausgelegt“
PR
Im Moment reicht das. Wichtig ist, dass wir jetzt das Know-how haben und in der Lage sind, selbst zu bestimmen, wie es weitergeht. Der nächste Schritt ist nun, das, was wir tun, verstärkt zu kommunizieren.
Lassen Sie uns über die Details der Konstruktion sprechen. Es handelt sich um ein integriertes Chronographenkaliber mit Kugellagerrotor und Schaltrad – ich nehme an, all das war von vornherein selbstverständlich?
Ja.
Warum haben Sie sich für eine vertikale Kupplung entschieden?
Weil wir vermeiden wollten, dass der Chronographenzähler beim Starten springt.
Und warum für einen beidseitig aufziehenden Rotor?
(Lacht.) Ich weiß, das ist manchmal ein Glaubensstreit zwischen den Uhrmachern. Ein beidseitiger Aufzug ist symmetrischer und leicht effizienter. Wenn der Rotor nicht frei und einseitig schwingt, sondern eben beidseitig aufzieht, trägt sich die Uhr auch bedeutend angenehmer.
Sie haben sich also nicht etwa am Valjoux 7750 orientiert, dessen Rotor ja in eine Richtung aufzieht?
Nicht im Hinblick auf den Aufzug. Hinsichtlich der Abmessungen haben wir es allerdings als Vergleich herangezogen und gesagt, wir wollen bei der Höhe mit einem Millimeter weniger auskommen.
Aus ästhetischen Gründen, damit die Uhr flacher wird?
Ja. Am Ende sind es nun statt 7,9 Millimeter 7,2 geworden. Für 6,9 Millimeter hätten wir Kompromisse eingehen müssen, und das wollten wir nicht. Wir wollten etwas Robustes.
Die Gangautonomie ist mit 70 Stunden sehr hoch. Warum war Ihnen das wichtig?
Zum einen können Sie die Uhr am Freitag ausziehen, und am Montagmorgen läuft sie noch. Sie müssen sie nicht neu einstellen. Zum anderen bewirkt eine höhere Gangautonomie eine höhere Amplitude und einen stabileren Gang.
Wodurch haben Sie die höhere Gangautonomie erreicht?
Durch eine längere und gleichzeitig breitere Zugfeder und durch die Reduzierung von Reibung im Räderwerk.
Viele neu konstruierte Werke verfügen über eine frei schwingende Unruhspirale. Sie setzen stattdessen auf eine Feinregulierung über Rücker und Exzenterschraube – warum?
Wir haben gute Erfahrungen mit dieser Art des Regulierens gemacht, auch im Hinblick auf die Chronometerprüfungen der COSC. Da haben wir die Zuverlässigkeit dem Neuen vorgezogen. Eine pragmatische Entscheidung: Wenn etwas gut läuft, wollen wir es nicht ändern.
Das Breitling 01 hat auch ein stoßgesichertes Ankerrad.
Das ist ein Vorteil, wenn es zu Stößen kommt. Jedoch ist es bei dieser Konstruktion schon fast ein kleiner Luxus, da es mehr als 100 Prozent an Zuverlässigkeit bietet.
Dem 2009 vorgestellten Kaliber 01 folgten zunächst Kaliber 04 mit zweiter Zeitzone und Kaliber 05 mit Weltzeitindikation.
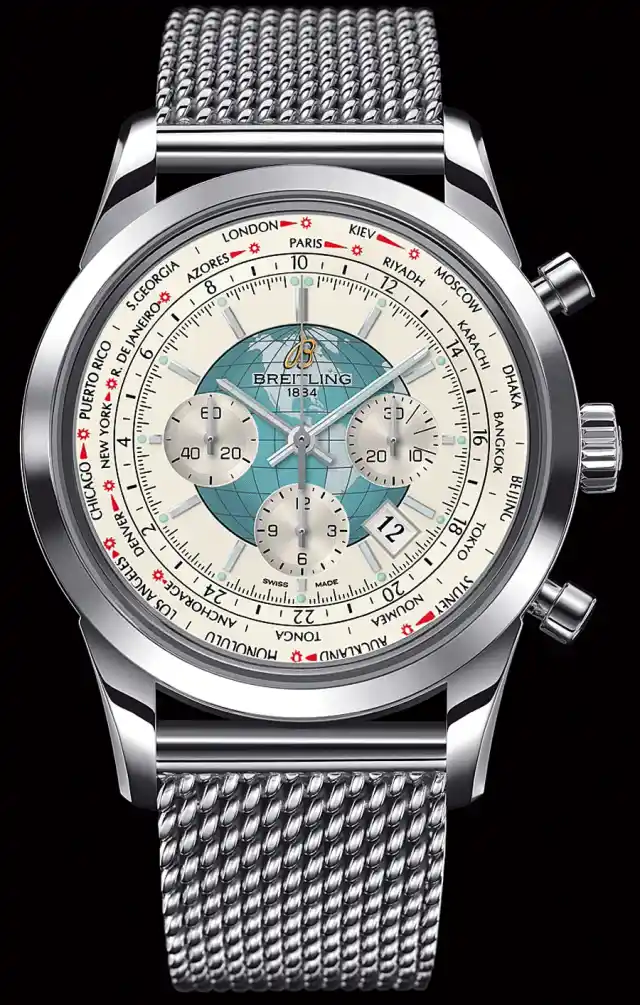
Genial einfach: Bei der Weltzeituhr Unitime lassen sich alle Funktionen über die Krone einstellen
PR
Unsere Losung lautet: „Instruments for Professionals“. Also nicht: sehr komplizierte Uhren in kleinen Stückzahlen, sondern: nützliche Funktionen mit einfacher Bedienung, als Bestandteil der normalen Kollektion. Die zweite Zeitzone ist eine nützliche Funktion für Leute, die viel reisen. Für dieses Kaliber haben wir eine spezielle Konstruktion mit einem Differenzial entwickelt. Diese Technik erlaubt es, dass alles über die Krone eingestellt wird. Der Stundenzeiger wird separat verstellt, sodass Sie die genaue Zeit nicht verlieren. Und wenn Sie den Stundenzeiger so oft drehen, dass ein neuer Tag angezeigt wird, dann springt auch das Datum weiter. Das funktioniert in beiden Richtungen.
Differenziale werden meist für Gangreserveanzeigen eingesetzt.
Genau. Daher kennt man das. Das Problem bei einem Differenzial ist, dass viele Räder involviert sind, es gibt also viel „Spiel“. Bei einer Gangreserveanzeige ist das unproblematisch. Aber in unserem Fall müssen die Indikationen der 12 und der 24 Stunden sehr präzise synchronisiert sein.
Wie haben Sie das Problem gelöst?
Wir haben einen eleganten Mechanismus gefunden, um diese „Spiele“ immer auf eine Seite zu ziehen. Das haben wir patentieren lassen.
Den gleichen Mechanismus verwenden Sie für die Weltzeituhr.
Ja, Kaliber 05. Hier gibt es ein weiteres Patent: Normalerweise ist der Städtering nicht mit dem Werk verbunden, sondern mit der Krone oder einem Drücker oder direkt mit einer Drehlünette. Bei uns ist der Städtering mit dem Satellitenrad des Differenzials verkuppelt. Wenn Sie also beispielsweise von Europa nach New York fliegen, drehen Sie einfach die Krone so weit, dass New York ganz oben bei der Zwölf steht. Der Stundenzeiger bewegt sich automatisch mit. Die genau eingestellte Uhrzeit bleibt erhalten, und falls der Chronograph läuft – kein Problem. Sie können dabei am Werk nichts kaputtmachen. Damit zeigen wir unsere Innovationskraft auch bei Komplikationen: Einen so einfach zu bedienenden Chronographen mit Weltzeitfunktion gab es bisher nicht; das ist eine Weltneuheit.
Dann gibt es das Kaliber 02: einen Handaufzugs-Chronographen mit 24-Stunden-Anzeige.
Dieses Modell bezieht sich auf die erste Variante unserer Cosmonaute mit 24-Stunden-Anzeige, die 1962 von Scott Carpenter während seiner Raumfahrtmission getragen wurde: Sie hatte ebenfalls zuerst ein Handaufzugswerk, später gab es sie auch mit einem Automatikwerk von Dubois Dépraz.
Wird es auch ein Dreizeigerwerk geben?
Gute Frage. Wenn wir ganz unabhängig sein wollen, brauchen wir auch ein Dreizeigerwerk.
Das heißt, Sie haben sich noch nicht definitiv entschieden?
Doch, aber das Thema ist nicht so einfach.
Können Sie nicht Ihr Kaliber 01 als Basis nehmen und es um die Chronographenfunktionen reduzieren? Mit dem 7750 wird mitunter so verfahren.
Das wäre das Einfachste, aber es wäre keine optimale Lösung und würde daher nicht zu Breitling passen. Die Zugfeder und damit die Bauhöhe wären zu hoch, der Durchmesser mit 30 Millimetern auch sehr groß. Es wäre ein Kompromiss, und Kompromisse wollen wir nicht eingehen. Nein, wenn wir ein Dreizeigerwerk entwickeln, muss das auf dem gleichen Niveau sein wie unser Chronographenkaliber. Das Problem ist aber nicht die Technik, sondern die Kosten. Wir verkaufen weit weniger Dreizeigeruhren als Chronographen. Auf der anderen Seite ist die Zahl der Dreizeigerwerke in der gesamten Schweizer Uhrenindustrie viel höher. Dieser beträchtliche Unterschied bei den Stückzahlen stellt für uns eine echte Herausforderung dar, ein gutes Preis-Leistungs-Verhältnis anbieten zu können.
Muss denn ein neues, eigenes Dreizeigerwerk auch auf verschiedene Komplikationen ausgelegt sein?
Ja, aber nicht auf so viele wie der Chronograph. Sagen wir so: Eine GMT-Funktion passt auch gut in eine Dreizeigeruhr, aber grundsätzlich erwarten unsere Kunden bei einem komplizierteren Zusatzmechanismus schon die Verbindung mit einem Chronographen.
Nach der Mitteilung der Schweizer Wettbewerbskommission vom 15. Mai ist die Belieferung von Uhrwerken durch die Eta vorerst bis Ende 2013 gesichert. Wann könnten Sie eine komplette Einstellung der Lieferung durch eigene Kaliber vollständig kompensieren?
Wenn das wirklich nötig wäre, könnten wir in zwei, drei Jahren so weit sein. Wir müssten dann in La Chaux-de-Fonds erneut anbauen, um die Produktionsfläche zu vergrößern.
Auch für Ihre eigenen Kaliber benötigen Sie Teile von der Swatch Group wie Anker, Ankerrad und Spirale. Gibt es Pläne, auch solche Teile selbst zu produzieren?
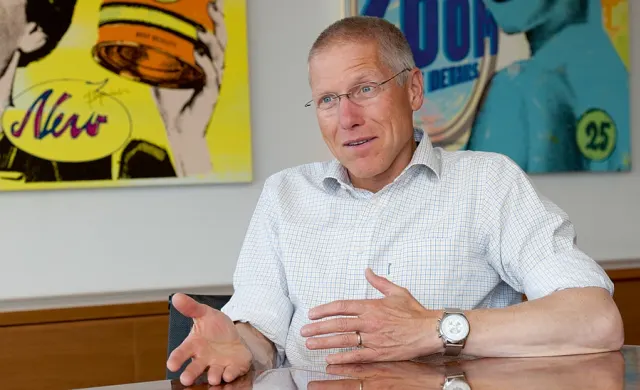
Girardin: "Das Thema ,Swiss made', im Sinne von zu 100 Prozent hergestellt in der Schweiz, ist uns sehr wichtig."
PR
Was Spiralfedern angeht, so gibt es mittlerweile neben der Nivarox auch andere Hersteller, die das nicht so schlecht machen. Wir haben bereits einige davon getestet. Bei den anderen Komponenten sind wir dran.
Sie wollen Anker und Ankerrad mittelfristig selbst herstellen?
Ja. Man muss aber wissen: Es ist ein Unterschied, ob man Anker und Ankerrad so produziert, dass sie eine Uhr einfach nur zum Laufen bringen – oder ob man sie für Werke produziert, die zu 100 Prozent chronometerzertifiziert werden sollen. Das ist wesentlich schwieriger.
Mit wie vielen Jahren rechnen Sie, bis Sie so weit sind?
Mit einigen Jahren muss man schon noch rechnen.
Einige Ihrer Mitbewerber setzen auf Spiralfedern aus Fernost. Wäre das für Sie ein Thema?
Nein. Wir beziehen unsere Komponenten nur aus der Schweiz. Das Thema „Swiss made“, im Sinne von zu 100 Prozent hergestellt in der Schweiz, ist uns sehr wichtig.
Wäre es für Sie ein Thema, eigene Spiralfedern herzustellen?
Nein, das lohnt sich nicht. Wir könnten die Maschinen nicht ausreichend auslasten. Aber wir müssen auch nicht alles selbst machen. Im Prinzip brauchen wir ein, zwei gute, hoch spezialisierte Lieferanten – so, wie es bei Gehäusen, Zeigern, Zifferblättern oder Schrauben der Fall ist. Wir wollen dazu beitragen, diesen eine gewisse Kapazität zu geben und sie so zu unterstützen. Es gibt so viele hervorragende Spezialisten in der Schweiz. Ohne ihre Mithilfe hätten wir unser eigenes Kaliber nicht produzieren können. Was konkret die Spiralfedern angeht, ist es auch denkbar, dass wir nur lose Spiralfedern zukaufen und den Rest selbst herstellen. Schon jetzt fertigen wir zum Teil eigene Unruhreife und sind in der Lage, die schwierige Operation des Anschweißens der Spiralfedern an die Spiralrollen auszuführen.
Können Sie einen Überblick geben: Welche Teile fertigen Sie selbst?
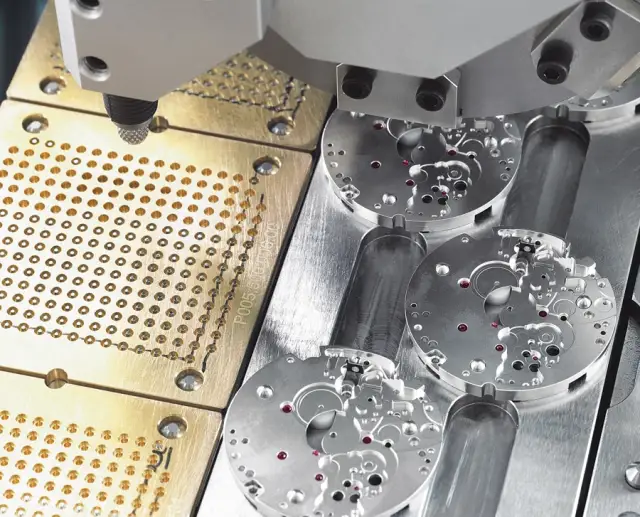
In-house-Produktion: Strategisch wichtige Teile wie Brücken und Platinen stellt Breitling selbst her
PR
Die Messingteile für das Rohwerk fertigen wir selbst: also Brücken und Platinen, aber auch die Kalenderscheiben. Auch die Vormontage geschieht in-house, ebenso sind die Bereiche Forschung, Entwicklung und Labor bei uns angesiedelt. Was wir nicht zu 100 Prozent machen, sind alle gestanzten Stahlteile. Hier fertigen wir die Komponenten für die Prototypen selbst, aber die Teile für die Serienproduktion kaufen wir. Ähnliches gilt für die Drehteile: Achsen, Schrauben, Räder – und auch für die Dekoration, etwa die Galvanik. Dafür gibt es ebenfalls gute Spezialisten.
Breitling steht für sportliche Chronographen mit typischem Look. Das gilt sowohl für die Chronomat mit ihren Lünettenreitern als auch für die Navitimer mit ihrer Rechenschieberlünette. Vor einigen Jahren haben Sie diese Optik ergänzt durch die Superocean-Modelle. War es nicht ein Risiko, auf einmal ein Retro-Design einzusetzen?
Das klassische Design der Superocean-Modelle ist sehr erfolgreich. Es stammt ja aus den fünfziger Jahren, ist aber letztlich sehr modern. Generell waren die Fünfziger ein gutes Jahrzehnt fürs Uhrendesign.
Glasböden findet man bei Breitling selten. Ist nicht das eigene Kaliber ein Anlass, mehr Uhren mit Glasböden anzubieten?
Wir haben in den Linien Navitimer und Chronomat verschiedene limitierte Serien mit Glasboden herausgebracht. Und die neue Transocean mit Weltzeitfunktion kommt serienmäßig mit Glasboden. Aber generell waren Glasböden nie unser Thema.
Aber würde sich das eigene Kaliber nicht dazu anbieten?
Sicher ist das Kaliber 01 ein schönes Werk, das sich sehen lassen kann. Aber bei Breitling sollten Glasböden eine Exklusivität bleiben.
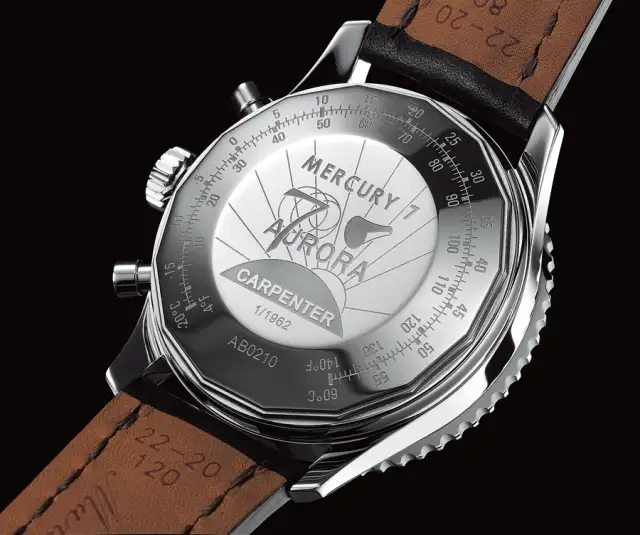
Gravierter Boden der Navitimer Cosmonaute: Glasböden bleiben bei Breitling eine Ausnahme
PR
Sie lassen, wie gesagt, jede einzelne Uhr als Chronometer zertifizieren, Mechanikuhren wie Quarzuhren. Hätten Sie Wünsche an die COSC, etwas an ihren Tests zu verändern?
Nein. Was die COSC einzigartig macht, ist ihre Unabhängigkeit und Objektivität: Es gibt keine andere Institution, die so viele einzelne Werke testet und die selbst wiederum regelmäßig von der Schweizerischen Akkreditierungsstelle (SAS) zertifiziert wird. Die Tests basieren alle auf einer ISO-Norm. Diese Prüfung durch eine unabhängige Institution ist uns sehr wichtig. Natürlich kritisieren manche, dass die COSC nur Werke testet, nicht Uhren, das heißt, dass die Werke erst nach dem Test in die Uhren eingeschalt werden. Aber da steht die jeweilige Marke in der Verantwortung, darauf zu achten, dass das Werk in der Uhr seine Ganggenauigkeit behält und dass die Uhr nicht etwa monatelang im Schaufenster unter einer Lampe steht. Und nach dem Verkauf liegt die Verantwortung wiederum beim Käufer, dass er die Uhr nicht fallen lässt, sie regelmäßig zum Service bringt etc. Auf der anderen Seite wird es einem gut ausgebildeten Uhrmacher immer möglich sein, ein COSC-zertifiziertes Werk wieder so einzuregulieren, dass es Gangwerte im Chronometerbereich bringt. Auch darin liegt der langfristige Mehrwert eines Chronometers mit COSC-geprüftem Werk.
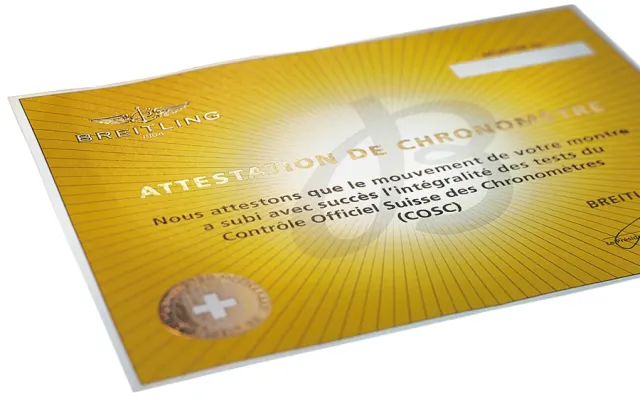
Breitling lässt alle seine Werke von der offiziellen Schweizer Prüfstelle COSC als Chronometer zertifizieren
PR
Welche Rolle spielen Quarzuhren – jetzt und in Zukunft?
Quarzuhren sind für uns nicht unwichtig, da wir mit Quarz neue Funktionen einführen können. Denken Sie nur an die Breitling Emergency mit dem Notrufsender. Quarzuhren stehen auch nicht in Konkurrenz zu mechanischen Uhren. Es gibt eben Kunden, die eine sehr hohe Präzision wünschen. Und eine Quarzuhr brauchen Sie im Prinzip nur zweimal im Jahr zu stellen, beim Wechsel von Sommer- und Winterzeit. Bei unseren chronometerzertifizierten Superquarzuhren macht zudem die Gangabweichung in sechs Monaten nur fünf bis sieben Sekunden aus.
Welches sind für Sie die strategisch wichtigen Preisbereiche?
Als wir 2009 die neue Chronomat mit Manufakturwerk einführten, mit veränderten Gehäusen und Zifferblättern, sind wir von rund 6.000 auf rund 8.000 Schweizer Franken gegangen. Das war eine andere Stufe. Das ist das Preissegment, in dem wir mit unseren Uhren mit eigenem Kaliber bleiben wollen. Die Transocean ist mit rund 10.000 Franken etwas teurer, aber sie bietet auch viele Funktionen und ist, wie oben erwähnt, eine einzigartige Uhr. Die große Herausforderung für uns liegt jetzt darin, dass diese neue Positionierung verstanden wird. Das müssen wir entsprechend kommunizieren und erklären. Und als unabhängige Marke muss man noch mehr kämpfen auf dem Markt.
Sicher hat Ihnen auch die Serie Breitling for Bentley geholfen, Breitling in höheren Preisregionen anzusiedeln?
Ja. Auf einmal haben sich Kunden für die Marke interessiert, die sonst keine Breitling-Käufer waren. Darüber hinaus haben wir mit Breitling for Bentley ein eigenes, sehr spezielles Design eingeführt und nicht etwa nur ein Bentley-Logo aufs Zifferblatt gebracht. Ein Grund für den Erfolg war sicherlich, dass wir Breitling for Bentley wie eine eigene Marke führen. Es gibt Juweliere, die führen Breitling, aber nicht Breitling for Bentley.
Werden Sie auch dort eigene Kaliber verwenden?
Das könnte sein, ja.
Wie stark ist bei Ihnen das Segment Golduhren?
Gut, aber wir sind bei den Stückzahlen noch nicht ganz da, wo wir hinwollen.
Woran liegt das?
Die Uhren sind sehr schwer, zumindest, wenn sie auch ein Goldband haben. Da wiegt eine Uhr schon mal 300 Gramm. Das wird von manchen Kunden als zu schwer empfunden. Und durch den hohen Goldpreis sind diese Modelle auch zwangsläufig teurer geworden. Aber wir sind dabei, in Sachen Gewicht eine Lösung zu finden.
Wie wichtig sind Damenuhren bei Breitling?
Immer mehr Frauen tragen große Uhren, daher sind sie als Kundinnen wichtig. Auf der anderen Seite bewegen wir uns im Segment von technischen, funktionalen Uhren. Klassische kleinformatige Damenuhren gehören nicht dazu. Die Größe unserer Uhren richtet sich in gewisser Weise auch nach der Funktion. Ein Chronograph beispielsweise braucht eine gewisse Mindestgröße, sonst ist er nicht mehr ablesbar. Wir werden also nie kleine Chronographen bringen. buc
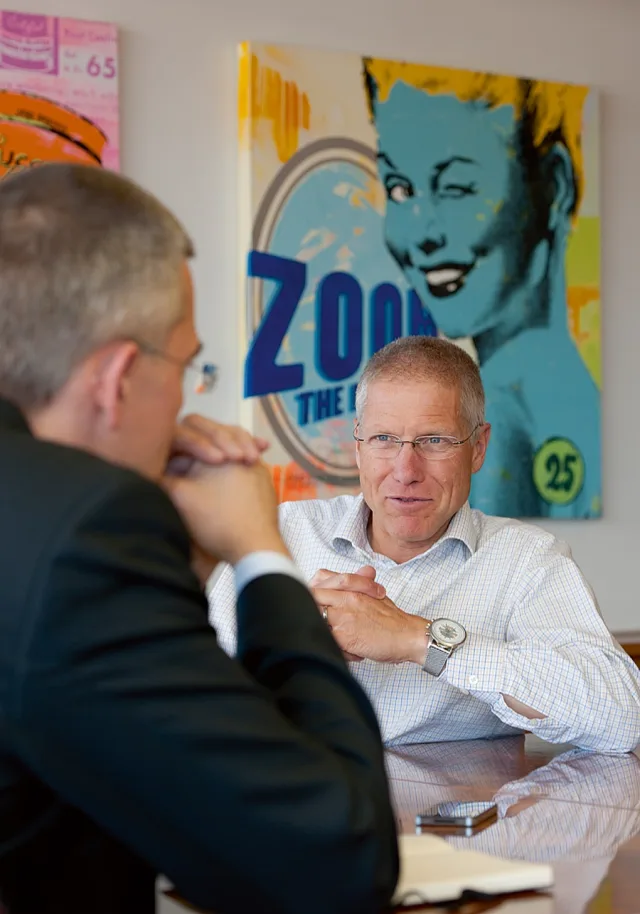
Jean-Paul Girardin im Gespräch mit Rüdiger Bucher
PR
Fotos: Eveline Peroud und Breitling
Sie möchten mehr über die Uhrenmarke Breitling wissen?
Dann bestellen Sie doch das Chronos Sonderheft Breitling mit über 140 Seiten über den Chronographenspezialisten.
Das Sonderheft ist ab sofort unter das unter www.watchtime.net/shop “Chronos” erhältlich