Sie halten zusammen, was zusammengehört: Zwischen Platine, Brücken und Kloben drehen und schwingen die Komponenten des Uhrwerks. Das Trio ist nicht nur funktional, sondern bietet auch etwas für das Auge.
Alles ruht auf ihr: die Grundplatine, auch Werkplatte genannt, ist die Basis eines jeden Uhrwerks. Alle Komponenten und Mechanismen des Werks werden darauf aufgebaut, denn die Montage des Uhrwerks beginnt stets mit der unteren Platine, die schließlich direkt hinter dem Zifferblatt der fertigen Uhr zum Liegen kommt. Hier ruhen die Wellen des Räderwerks, dienen eingepresste Steinlager oder gar verschraubte Chatons der Aufnahme von Zapfen, lassen Ausdrehungen den sich hier später drehenden Zahnrädern ausreichend Platz. Wenn die Platine die Basis ist, dann sind Brücken und Kloben der krönende Abschluss. Sie übernehmen auf der Oberseite die Funktion des Gegenparts zur Platine und dienen als Lagerträger für die Räderwellen.

Der Anfang: Als Rohmaterial für Platine, Kloben und Brücken dient eine Messingronde mit Haltenut
PR
Eine bekannte und besondere Variante ist die sogenannte Dreiviertelplatine, welche 1864 von Ferdinand Adolph Lange eingeführt wird. Sie bildet das Gegenstück zur Werkplatte, überdeckt allerdings nur drei Viertel des Werks. Zwischen der Werkplatte und der Dreiviertelplatine sind das Räderwerk, Federhaus und Kronrad gelagert; die Lagerungen der Unruh und des Ankers befinden sich in einem Kloben. Befürworter dieser Bauweise sagen, dass diese Konstruktionsform im Vergleich zu Einzelbrücken ein Uhrwerk stabiler mache. Die Dreiviertelplatine findet sich bei historischen Taschenuhren aus England, Amerika und Glashütte sowie heute wieder bei modernen Armbanduhrwerken aus Glashütte, zum Beispiel bei Nomos.
Kloben liegen anders als Brücken einseitig auf der Platine auf
Ein Werk, dessen Oberseite nur mit Brücken und Platinen gestaltet ist, bietet zum Beispiel schönere Einblicke in das Werk. Zudem gibt es nach dem Zusammenbau mehr Möglichkeiten zur Kontrolle und Korrektur. Der entscheidende Unterschied zwischen Brücken und Kloben ist, dass Brücken an beiden Enden auf der Grundplatine aufliegen und dort mit Stellstiften und Schrauben fixiert sind; Kloben liegen hingegen einseitig auf der Platine auf, sind meist mit nur einer Schraube befestigt und kragen über die Werkplatte aus. In der Regel werden Kloben vor allem als Lagerung für die Unruhwelle genutzt. Brücken werden häufiger benötigt: In einem Standardwerk kommen normalerweise vier Brücken zum Einsatz – für Federhaus, Unruh, Räderwerk und Anker. Es ist üblich, die Brücken nach den Teilen zu bezeichnen, denen sie als Lager oder Stütze dienen, wie die Federhausbrücke oder die Minutenradbrücke. Anzahl und Form der Brücken bestimmt der Hersteller nach ästhetischen und ökonomischen Gesichtspunkten – mehr Brücken bedeuten auch höhere Fertigungskosten.
Wo gedreht wird, fallen Späne: An der Drehbank wird die Dreiviertelplatine aus der Ronde geschnitten
PR
Brücken sind an der Unterseite ausgefräst und tragen die Lagersteine zur Aufnahme der oberen Zapfen der Räder. Außerdem tragen sie an ihrer Unterseite – ebenso wie Kloben – Passstifte, die genau in entsprechende Bohrungen der Platine passen und für den korrekten Sitz am richtigen Platz sorgen. Platinen, Brücken und Kloben haben einiges gemeinsam: Sie sind – wie beschrieben – anspruchsvoll im Aufbau, und sie müssen in jeder Hinsicht maßgefertigt sein – mit Toleranzen im Bereich von nur Tausendstel Millimetern.
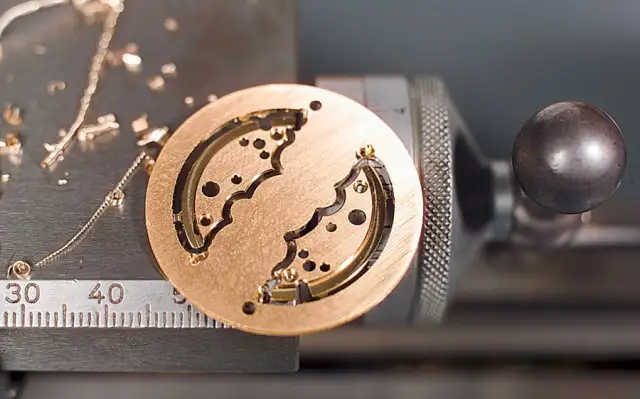
Automatikbrücke: Zwei fertig gefräste Automatikbrücken vor dem Heraustrennen aus dem Haltering
PR
Auch das Material will gut ausgewählt sein: In der Regel bestehen Platinen, Brücken und Kloben aus Messing, also einer Kupfer-Zink-Legierung; bisweilen wird eine Platine auch aus Neusilber, einer Kupfer-Nickel-Zink-Legierung, gefertigt. Gemeinsam sind ihnen auch die Arbeitsschritte, die bei der Herstellung zu vollbringen sind und anhand von Komponenten erklärt werden, die bei Nomos entstehen: Die Glashütter Marke fertigt unter anderem die Werkplatte, die Dreiviertelplatine, den Unruh und den Ankerkloben sowie die Automatikbrücke selbst.
Brücken und Kloben bestehen meist aus Messing
Am Anfang steht der Computer: Hier werden die exakten Konstruktionszeichnungen jedes Einzelteils mit Maßangaben erstellt und schließlich in ein Computerprogramm zur Steuerung von CNC-Fräsautomaten übertragen. Diese Maschinen sind wahre Wunderwerke: Computergesteuert werden alle Seiten eines Werkstücks bearbeitet, mit bis zu 96 verschiedenen Werkzeugen wird gefräst, gebohrt und geschnitten. In einem Arbeitsgang können 20 Werkteile bearbeitet werden, was je nach Komplexität des Werkstücks zwischen zweieinhalb und sieben Stunden dauern kann.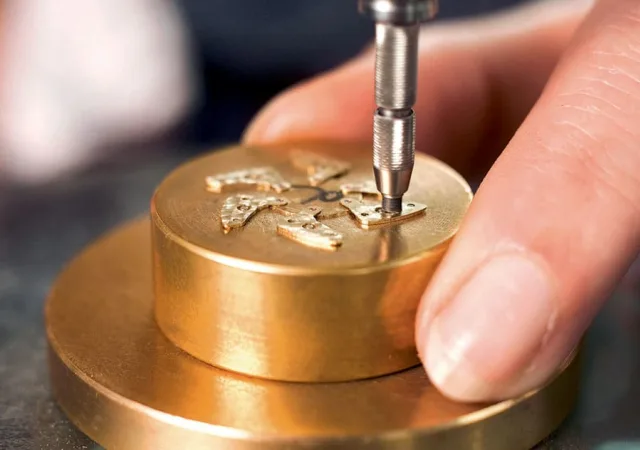
Beim Perlieren der Ankerkloben wird ein diamantgebundener, rotierender Gummistift von Hand kreisförmig über die Oberfläche der Werkteile bewegt
PR
Rohmaterial sind Messingronden, die bereits so bearbeitet sind, dass sie exakt die gewünschte Stärke aufweisen und absolut parallel und plan sind. Ihr Durchmesser übersteigt den der zu fertigenden Teile – der Überstand dient als Haltering, damit der Rohling während der Bearbeitung fixiert werden kann. Nach dem Fräsen ist dieser Haltering nicht mehr erforderlich, und die Teile werden herausgebrochen. Aus einer Ronde werden vier Kloben, zwei Automatikbrücken oder eine Dreiviertelplatine gefertigt, die nun penibel gereinigt und kontrolliert werden. Dann ist der Moment gekommen, da sie auf dem Werktisch eines Handwerkers landen. Jedes Teil wird von Hand fein bearbeitet. Dann erhält es mittels Sandstrahlen – dabei wird feines Bronzepulver aufgeblasen – eine samtige, glatte Oberfläche.

Mit Blick durch ein Mikroskop graviert man Unruhkloben. Der Handwerker schneidet dabei mit einem Stichel Ornamente in das Metall
PR
In der Vormontage werden die Lagersteine aus synthetischem Rubin pneumatisch in vorgebohrte Löcher gelegt und eingepresst, ebenso die Pfeiler und Stifte. Zuletzt geht es um die Schönheit, also um Dekoration und Zierschliffe, die zum großen Teil nach alter Uhrmacher-Tradition aufgebracht werden. Bei Nomos werden die Oberfläche des Ankerklobens sowie die Werkplatte perliert. Andere Teile wie Dreiviertelplatine oder Unruhkloben tragen den Glashütter Bandschliff, der den Genfer Streifen entspricht. Ein Unruhkloben für ein Tonneau-Kaliber bekommt als i-Tüpfelchen ein handgraviertes Muster.
Zuletzt werden Brücken und Kloben verziert
Die Dreiviertelplatine erfährt eine weitere Behandlung: Der Namenszug wird eingraviert, nach der galvanischen Vergoldung mit Lack überzogen und schließlich galvanisch rhodiniert. Wegen des Lacks bleibt die Schrift ausgespart, sodass der Namenszug nun golden auf dem weißen Rhodium prangt. Auch die anderen Teile werden im galvanischen Bad vollendet und erhalten eine Rhodiumschicht, die nicht nur der Schönheit, sondern auch dem Schutz des Ausgangsmaterials Messing dient. Da diese Schichten mit nur einigen Tausendstel Millimetern hauchdünn sind, bleiben anschließend die aufwändigen Zierschliffe gut sichtbar.
Tourbillon unter drei Goldbrücken von Girard-Perregaux
Girard-Perregaux
Alle Gestellteile, die mit Fett und Öl in Verbindung kommen, wie Werkplatte und Dreiviertelplatine, werden zum Abschluss epilamisiert, also mit einem Überzug versehen, der das "Wegkriechen" dieser wichtigen Schmierstoffe verhindert. Der Aufwand, der bei der Dekoration von Uhrwerkteilen betrieben wird, zeigt, dass es sich um mehr als nur funktionale Werkkomponenten handelt. Sie tragen entscheidend zur optischen Wirkung bei. Und vor allem die Brücke tut sich als gestalterisches Element hervor: zum Beispiel im 1884 entwickelten Girard-Perregaux-Werk, das mit drei Goldbrücken aufwartet; oder in der Santos Dumont Skeleton von Cartier, in der die Brücken sich sogar zu römischen Ziffern formieren.

Die Brücken der Cartier Santos Dumont Skeleton formieren sich zu römischen Ziffern
PR
Brücken der besonderen Art bietet Corum in der Golden Bridge, einem legendären Modell, entworfen von Vincent Calabrese, das 1980 erstmals präsentiert wurde. Um die originelle Idee eines schmalen, stäbchenförmigen Uhrwerks umzusetzen, leistete Corum viel Entwicklungsarbeit: Jedes Einzelteil musste überdacht, neu konstruiert und miniaturisiert werden, bis zu guter Letzt ein 30 Millimeter langes Uhrwerk mit drei goldenen Brücken dabei herauskam, bei dem alle Komponenten in einer Reihe montiert waren.
Brücken tragen auch zur optischen Wirkung bei
Mittlerweile gibt es eine modernisierte Variante, die jedoch in der Herstellung nicht weniger aufwändig ist als das ursprüngliche Modell. Die wesentlichen Komponenten werden direkt von Corum gefertigt. Aus Platten in Weiß-, Gelboder Rotgold werden die stäbchenförmige Platine und die Brücken auf ihr perfektes Maß geschnitten. Mittels Drahterosion ist das möglich. Von Hand verfeinert und dekoriert – die Brücken etwa sind handgraviert – sorgen sie schließlich für den Zusammenhalt des Werks. Bis alle so entstandenen, in unserem Fall rund 140 Einzelteile perfekt ineinandergreifen, vergeht viel Zeit: Alleine die Produktion des Ebauches erfordere rund 150 Arbeitsschritte, heißt es bei Corum; Dekoration und Einschalen nehmen weitere drei Monate in Anspruch. Doch das Warten lohnt: Am Ende steht eine Uhr, deren Werk von allen Seiten bewunderungswürdig ist und die Mechanik zum Faszinosum macht – Brücken in ihrer schönsten Form.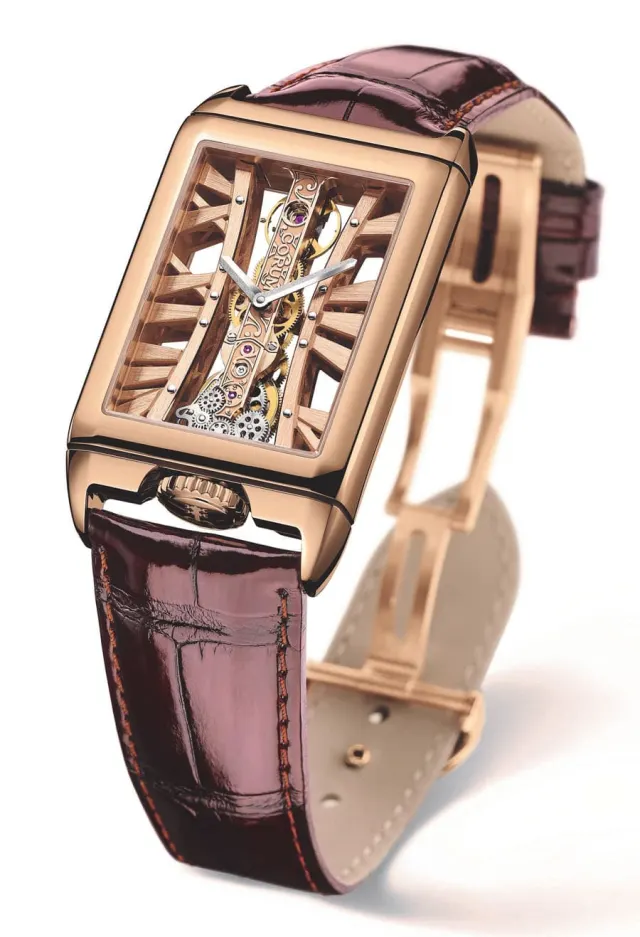
Corum: Golden Bridge Rectangle
PR
Auch die Uhrwerksschrauben sind wichtige Komponenten, die das Uhrwerk zusammenhalten. Mehr über diese kleinen, aber essentiellen, Uhrwerkteile erfahren Sie hier.