Ihm verdankt die Armbanduhr ihren Namen. Denn ohne Uhrenarmband wäre unser schönstes Stück schnell nicht mehr dort, wo wir es wünschen – am Handgelenk. Viel Liebe zum Detail und hohe handwerkliche Kunst sind für ein Armband nötig.
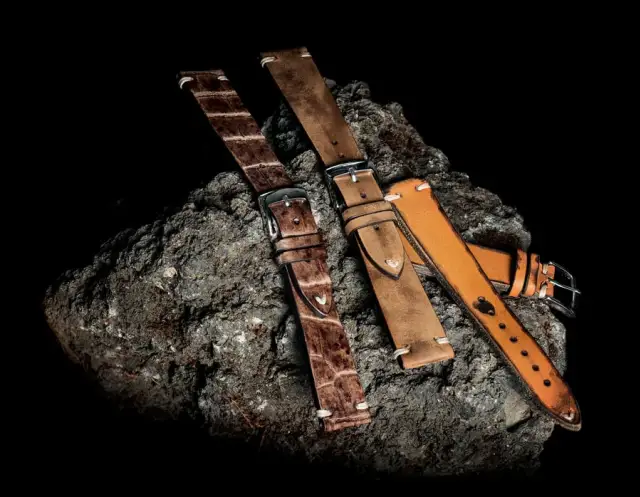
Handwerkskunst: Zu einer Manufaktur-Uhr passen keine Armbänder aus industrieller Fertigung
PR
Jana Osann kann es. Sie spannt mit ihren flinken Fingern das Uhrenleder ein und erläutert, was eine Sattlernaht ausmacht. Mit zwei Nadeln und einem Faden bewaffnet, geht es mit einer Art schneller und kraftvoller Schaukelbewegung wechselseitig durch das Armbandleder hindurch. Das geschieht mit der routinierten Leichtigkeit, welche die Beherrschung eines Handwerks erkenntlich macht. Die Jahrgangsbeste unter den Feintäschnerinnen bei der Uhrenarmbänderfabrik Kaufmann ist eine Botschafterin ihres Handwerks. Ihr ist ihre Tätigkeit erkennbar mehr Berufung als Beruf. Um ihren Abschluss zu erhalten, pendelte sie während ihrer Ausbildung immerhin 400 Kilometer.
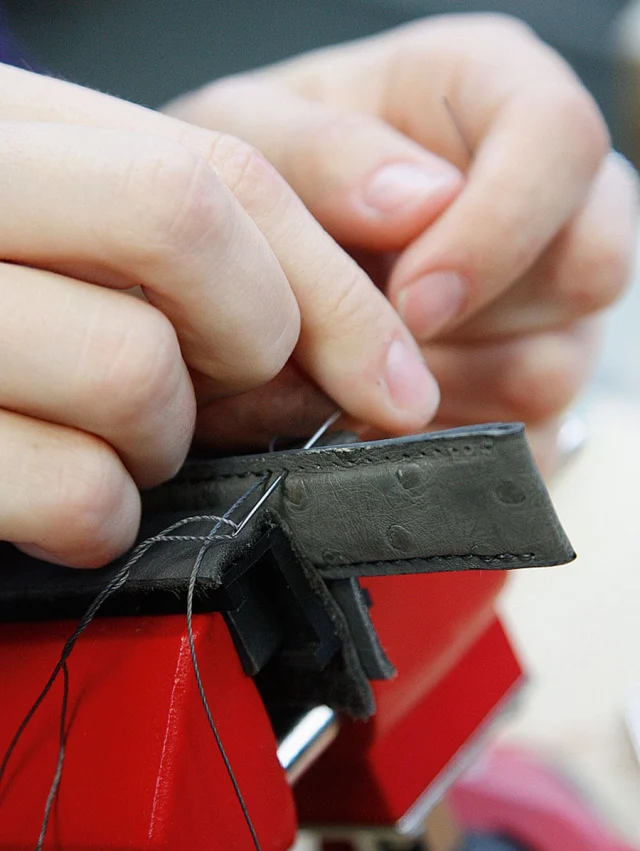
Sattlernaht: Mit zwei Nadeln, aber einem Faden werden Ober- und Unterseite vernäht. Das dauert je Band über eine halbe Stunde
PR
Denn Feintäschner sind mittlerweile so selten, dass sie gemeinsam mit anderen lederverarbeitenden Berufen wie Auto- und Reitsattlern zusammen die Berufsschulbank drücken müssen. Aber bevor ein Uhrenarmband überhaupt mit einer Sattlernaht vernäht wird, sind zuvor noch zahlreiche Arbeitsschritte notwendig. Davon überzeugen wir uns, indem wir selbst einige Schritte weiter durch die kleine Manufaktur in Mühlheim bei Frankfurt gehen.
74 Arbeitsminuten stecken in einem Uhrenarmband
Hier ist die Kaufmann Uhrenarmbänderfabrik in einem mittelständigen Gewerbegebiet ansässig. Seit 42 Jahren ist der Firmeninhaber im Unternehmen, jetzt ist sein Sohn, Philipp C. Kaufmann, angetreten, um das seit 72 Jahren bestehende Unternehmen in dritter Generation erfolgreich zu führen. Als Prokurist und geprüfter Betriebswirt hat er das Rüstzeug, aber auch den Respekt der Mitarbeiter, der dazu nötig ist.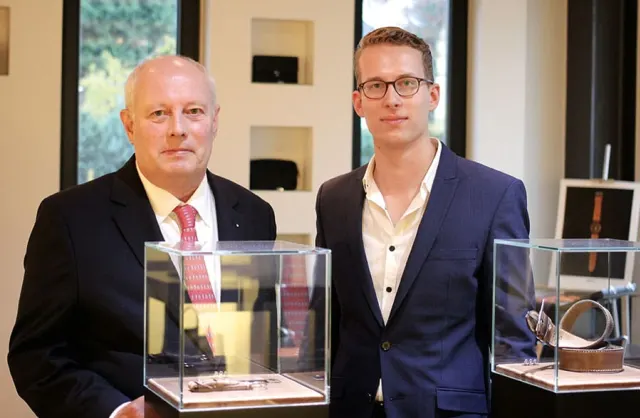
Gemeinsam: Vater Cornelius und Sohn Philipp Cornelius Kaufmann führen die Uhrenarmbandmanufaktur in Familientradition
PR
Vom hohen Fachwissen der Mitarbeiter können wir uns als nächstes an der Spaltmaschine überzeugen. Hier bekommen wir demonstriert, wie aufwendig die Herstellung eines Straußenlederarmbandes ist. Dafür wird das Leder abgehoben und peinlich genau vermessen. Nur wenn es die gewünschte Dicke von gerade einmal 0,85 Millimetern besitzt, ist es zur Weiterverarbeitung geschmeidig genug.
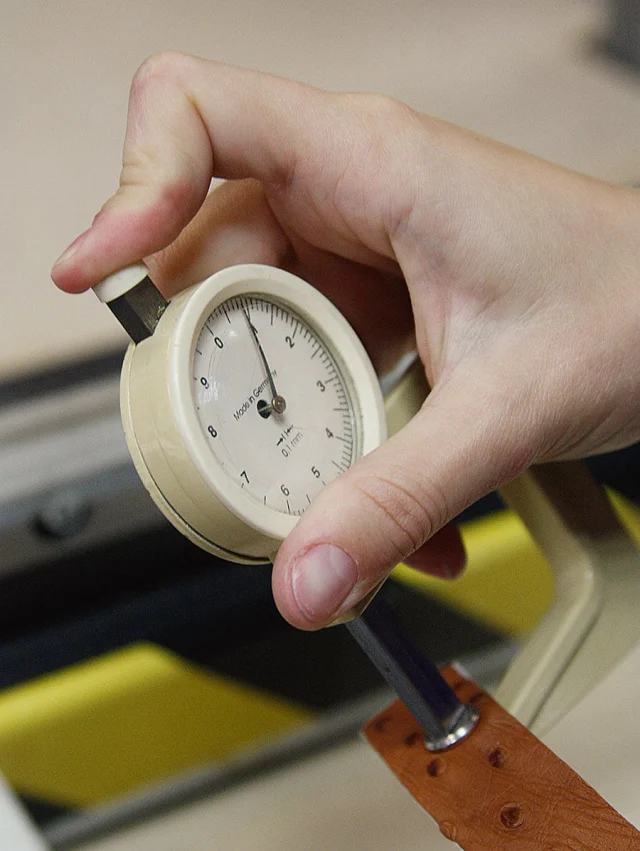
Messung: Akribisch wird das Straußenleder vermessen; nur 0,85 Millimeter darf es sein, um verabeitet werden zu können
PR
Die „quill marks", die markanten großen Löcher, welche die Straußenfedern in der Haut hinterlassen, werden alle einzeln und von der Unterseite mit passend ausgewählten kleinen Lederflicken von Hand ausgestopft. Verarbeitet werden bei Kaufmann viele unterschiedliche Ledersorten, wie der knapp 200 Seiten starke Katalog aufzulisten weiß.
Die Lederarmband-Manufaktur setzt auf Made in Germany
Vom Schweinsleder angefangen über Kalb, Jungstier, Ziege, Bison, Strauß, Haifisch, bis hin zu afrikanischer und Teju-Eidechse (letztere kennt man von Texas-Boots) reicht das Angebot der Uhrenarmbänder. Und natürlich krönt mattes und glanzgestoßenes Alligatorleder die Kollektion. Aber auch ausgefallene Ledersorten gehören zu den Kundenwünschen, die man hier erfüllt. Das bizarrste bisher angefragte Leder sei, das Stör-Leder. Originell in der Haptik, habe es sich leider als nicht ausreichend langlebig erwiesen.
Die bei Kaufmann verwendeten Leder für Uhrenarmbänder stammen weitestgehend aus Europa. Deren Qualität sei hier auf einem einmaligen Niveau. Die Kalbledergerberei steht in Furth im Wald. Nubukleder lasse man sich aus einer Familiengerberei aus Übersee zuliefern. Das Pferdeleder Shell Cordovan stammt aus den USA. Leider gebe es keine von den Luxusgüterkonzernen unabhängige Gerbereien mehr für Krokodilleder, bedauert Cornelius Kaufmann. Geschäftsführer Frank Kettering hält für uns ein Alligatorleder in die Höhe. Aus diesem rund anderthalb Meter langen Stück lassen sich nur acht Uhrenarmbänder stanzen. Bevor aus diesen Zuschnitten finale Uhrenarmbänder werden, sind noch viele Fertigungsschritte nötig.
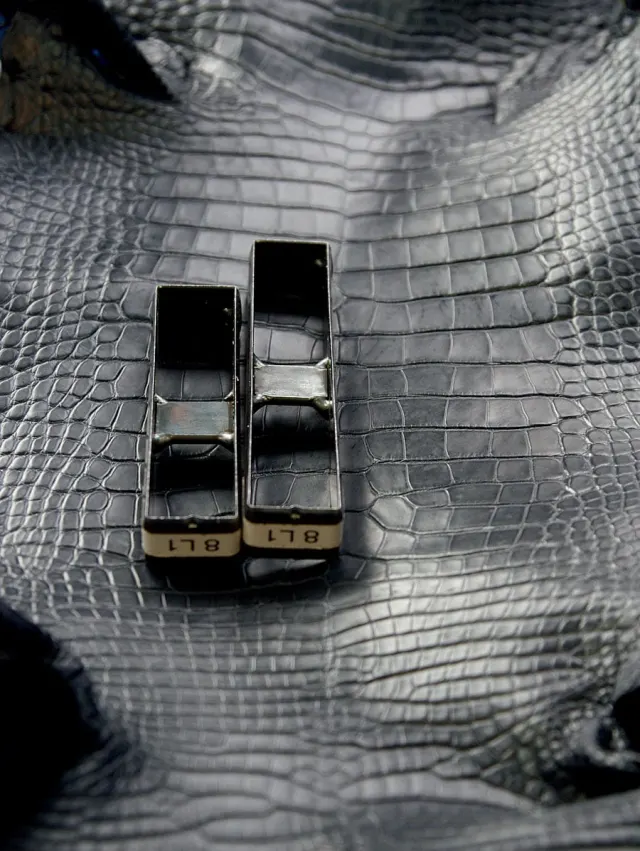
Alligator: Mit diesen Stanzformen werden die Zuschnitte aus dem Leder gefertigt. Ein Alligator ergibt durchschnittlich acht Bänder
PR
Insgesamt 104 Arbeitsschritte seien es genau, weiß Jana Osann zu berichten. Dazu zählen beispielsweise auch die Glasfasereinlagen, welche als Sicherungen in die Uhrenarmbänder an der Stelle eingenäht werden, die später den Federsteg beherbergt und damit der größten Belastung ausgesetzt ist. Die Füllung der bombierten Bänder wiederum besteht aus geformten Lederabfällen, weil diese als Polster besonders anpassungsfähig sind. Der Juniorchef Philip C. Kaufmann verrät einen kleinen Tipp, woran man echte Handarbeit erkennt.
Kaufmann-Uhrenarmbänder werden in Handarbeit gefertigt
Kritisch ist die Stelle der Schließenseite des Uhrenarmbandes, an der die Bandschlaufe eingenäht ist. Hier muss der Feintäschner mit Geschick die Nadel schräg führen, um an der Schlaufe vorbei zu stechen. Dazu ist eine Nähmaschine nicht in der Lage: Sie kann nur senkrechte Stiche und nimmt daher schnöde eine Abkürzung und beendet ihre Arbeit mit einer Quernaht vor der Schlaufe. Arbeitsgang für Arbeitsgang haben sich die Täschner von Kaufmann überlegt, wie man den Stolz der Manufaktur, das Excelsior-Band, noch aufwändiger und komplizierter herstellen kann. So wurde eine neue Arbeitstechnik für die Einlagen entwickelt. Die Handnaht des Uhrenarmbandes wird jetzt mit jeweils drei Stichen vom Nahtende zurückgenäht. Und noch nie wurden die Kanten des Bandes mit so viel Aufwand geschliffen und gefärbt. Es kommen drei verschiedene Schleifpapiere zum Einsatz, um die perfekte Bandkante zu erschaffen. Eigens neu entwickelte Arbeitsschritte sind nötig, das aufwändigste und komplizierteste Kaufmann-Band aller Zeiten zu kreieren: Kaufmann Excelsior.
Excelsior-Band: Der Stolz der Manufaktur ist dieses Lederband mit seiner besonders aufwändigen Verarbeitung der Kante
PR
Diese Liebe zum Detail ist typisch für Cornelius Kaufmann. Alles zu automatisieren wäre möglich, entspricht aber nicht seinem Qualitätsverständnis. Denn zum Gründungsmythos gehört die Geschichte seines Vaters Leo Kaufmann. Der Produzent feiner Gürtel verlor bei einer Wanderung in den Schweizer Bergen seine Uhr. Diese fand sich wieder und auch der Grund ihres Verschwindens war in einem fehlerhaften Band schnell ausgemacht. Daraus resultierte der Anspruch, die besten Lederarmbänder ihrer Zeit herzustellen. Mit den neuen Excelsior-Bändern demonstriert die Uhrenarmbandmanufaktur Kaufmann diesen Anspruch erfolgreich in der dritten Generation.