Es ist nicht alles durch und durch Gold, was glänzt: Gehäuse, Armbänder oder Werkteile können aus ästhetischen oder funktionellen Gründen mit Edelmetall überzogen werden. Dies geschieht durch Galvanisieren, einem vielseitig einsetzbaren Verfahren – etwa auch zur Rhodinierung.
Im 18. Jahrhundert wurde das Galvanisieren durch Zufall entdeckt
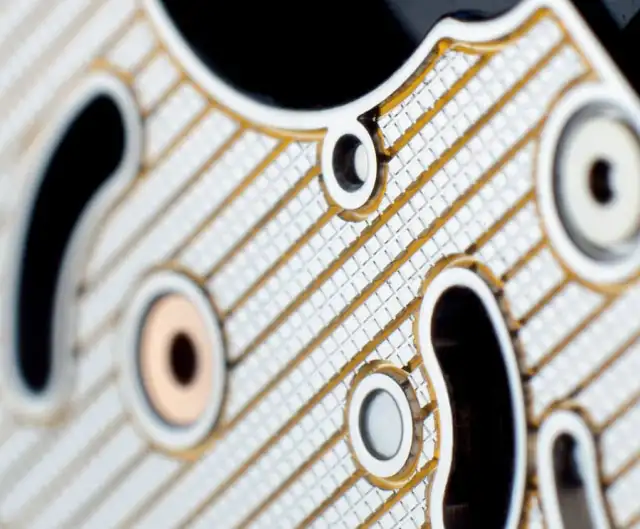
Eine galvanisierte Brücke im Uhrwerk
PR
Es klingt wie eine bizarre Fußnote der Wissenschaftsgeschichte, aber die Entwicklung der Galvanotechnik begann tatsächlich mit einem toten Frosch. Luigi Galvani entdeckte im 18. Jahrhundert beim Sezieren eben jenes Tieres etwas Ungewöhnliches: Wenn er das Bein des Frosches mit zwei verbundenen Drähten aus verschiedenen Metallen berührte, zuckte es. Galvani glaubte, eine neue Form der Elektrizität, die "tierische Elektrizität", entdeckt zu haben. Dies war ein Irrtum – allerdings ein folgenreicher. Denn Galvanis Experimente, bei denen die tierische Gewebeflüssigkeit quasi als Elektrolyt wirkte, führten zur Entwicklung der Galvanotechnik (früher auch Galvanostegie genannt), die ab etwa 1870 auch in industriellem Maßstab genutzt wurde.
Warum Galvanisieren?
Die dekorative Galvanisierung dient der Verschönerung, die funktionale dem Schutz vor Korrosion oder Verschleiß, der Katalyse oder der Verbesserung elektrischer Leitfähigkeit. Beispiele für die funktionale Galvanisierung sind die Verzinkung von Schrauben sowie die Vergoldung und Versilberung von elektrischen Kontakten. Davon profitieren heute viele Bereiche: In der Automobil- und der Luftfahrtindustrie werden viele verschiedene galvanisierte Teile benötigt. Das beschäftigt allein in Deutschland rund 1.500 Unternehmen, die Galvanisierungen durchführen.Galvanisierte Elemente steigern den Wert der Uhr
Nur ein Teil dieser Firmen ist in Sachen Schönheit tätig – der Bedarf an funktionaler Galvanotechnik ist um ein Vielfaches höher. Bei Schmuck und Uhren steigert die Galvanisierung nicht nur die äußeren, sondern auch die inneren Werte: Gehäuse und Bänder können galvanisch veredelt werden, was bei Gold als Plaqué bezeichnet wird (im Gegensatz dazu erfolgt beim Doublé die Vergoldung durch Aufschweißen und Aufwalzen), außerdem werden bei hochwertigen Uhrwerken Werkplatten, Kloben und Brücken galvanisch behandelt. Dabei geht es sowohl um besseres Aussehen als auch um Oberflächenschutz. Bis der Überzug in voller Schönheit erglänzt, bedarf es der entsprechenden Ausstattung und Erfahrung. Der Herr der Galvanikbäder ist der Galvaniseur. Er muss die Bäder ständig prüfen, ihren richtigen Säure- und Metallgehalt beobachten sowie das Aussehen, die Farbe und die Dicke der Metallschichten kontrollieren. Weiterführende Berufe sind Galvanomeister oder -techniker.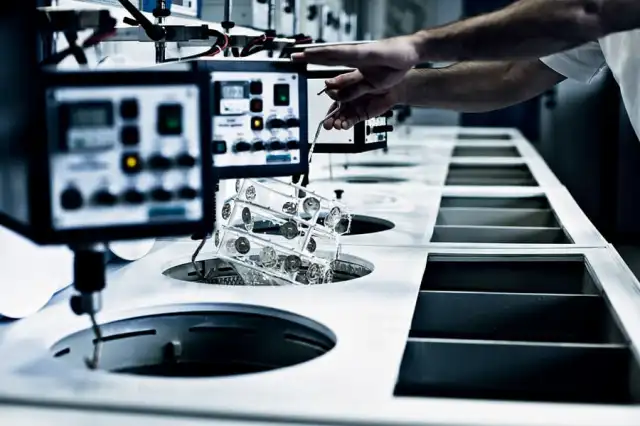
Hauseigene Galvanik bei Chopard: In langen Reihen stehen die Galvanikbecken, in welche die zu veredelnden Werkstücke über definierte Zeiträume eingetaucht werden
PR
Ein wichtiger Aspekt der Galvaniktechnik ist nicht nur ihre exakte Durchführung, sondern auch die korrekte Handhabung mit den Bädern. Deren Entsorgung unterliegt in Deutschland und anderen europäischen Ländern strengen Vorschriften, die hohe Folgekosten bedingen. Für die Abwässer gibt es streng geregelte Grenzwerte. Daher muss das Abwasser so lange behandelt werden, bis es unter diesen Grenzwerten ist. Erst dann darf es abgeleitet werden. Kleinere Unternehmen hingegen können die Galvanikflüssigkeiten extern entsorgen und müssen entsprechende Nachweise vorlegen.
Galvanisieren ist teuer
Ihren Preis haben auch die entsprechenden Anlagen. In der Regel bestehen sie aus einer Reihe von Wannen – bei der Gold- und Silberscheideanstalt C. Hafner in Pforzheim, die auch in der dekorativen Galvanik tätig ist, sind es etwa 150 Wannen auf einer Länge von insgesamt 70 Metern, in denen die verschiedenen Prozessschritte nacheinander erfolgen. Moderne Anlagen sind teilweise vollautomatisch gesteuert und können je nach Komplexität zwischen zwei oder drei Millionen Euro kosten. Eine einfache Ein-Liter-Anlage ist ab etwa 2.000 Euro erhältlich. In hochwertigen Anlagen läuft die Galvanik vollautomatisch ab, jeder Arbeitsschritt wird dabei systematisch protokolliert und aufgezeichnet.Die Uhrenmarke Lehmann Schramberg galvanisiert selbst
Bei der Uhrenmarke Lehmann in Schramberg, einem kleinen Ort im Schwarzwald, erfolgt das Galvanisieren in der eigenen Galvanik – durchgeführt von den Mitarbeitern selbst. Zuvor überantwortete man das Galvanisieren einer externen Firma. Uhrmacherin und Goldschmiedin Ulrike Scheller von Lehmann Schramberg erklärt bei einer Besichtigung der Manufaktur, dass aufgrund der längeren Arbeitswege häufig Teile oxidierten oder zerkratzten und somit unbrauchbar waren.
Galvanisieren von Hand: Mit Geduld und Sorgfalt nimmt ein Mitarbeiter bei Lehmann Schramberg die Galvanisierung vor
Copyright:48GradNord
Rainer Langenbacher
Deshalb beschloss man bei Lehmann, das Galvanisieren kleiner Stückzahlen selbst vorzunehmen. „Wir mussten viel ausprobieren und mit erfahrenen Leuten sprechen, bis wir die optimalen Arbeitsabläufe gefunden hatten. Schließlich sind wir keine ausgebildeten Galvaniseure.” Heute sind die Mitarbeiter in der Lage, Brücken und Platinen selbstständig zu galvanisieren. Nur das Beschichten der Zifferblätter sowie das Auftragen der Leuchtmittelfarbe auf die Zeiger und Indexe übernehmen weiterhin andere Firmen.
Wie Lehmann Schramberg die Brücken im Uhrwerk veredelt
Doch ohne entsprechende Vorbehandlung und Zwischenbearbeitung ist keine hochwertige Veredelung möglich. Bei Lehmann hat man sich zum Beispiel auf die aufwendige Veredelung von Brücken spezialisiert. Diese sind bei der deutschen Marke zweifarbig und tragen ein hochpräzises Waffelmuster, das in mehreren Schritten von Ultrapräzisionsmaschinen im eigenen Hause graviert wird. Lehmann ist nämlich auch Spezialist im Bau solcher Ultrapräzisionsmaschinen, die weltweit an namhafte Uhrenhersteller verkauft werden. Nach einer ersten Gravur werden die zu veredelnden Teile durch mehrere Reinigungsstufen im Ultraschallgerät und durch elektrolytische Entfettung penibel gesäubert und anschließend vergoldet. Damit ist die Oberfläche versiegelt. Der Großteil dieser Arbeitsschritte wird bei Lehmann manuell ausgeführt.
Die Brücken werden nach dem Vergolden von Hand ausgelackt, um die gwünschte Optik zu erzielen
PR
So werden die Brücken nach dem Vergolden von Hand ausgelackt, um ihre typische Zweifarbigkeit zu erreichen. Mit einer feinen Kanüle wird der Lack dazu vorsichtig in die Gravuren gefüllt. Eine Heizplatte sowie eine Vakuumpumpe helfen bei diesem Arbeitsschritt, das gewünschte Ergebnis zu erzielen. Der Lack hat sich dann gleichmäßig in die Rillen verteilt und die Entstehung von Luftblasen kann ausgeschlossen werden. Nun wird der Lack eingebrannt. Erst dann ist er so weit ausgehärtet, dass er die weitere mechanische und chemische Bearbeitung unbeschadet übersteht.
Warum man mit Rhodium galvanisiert
Anschließend vervollständigt eine weitere Gravur das Waffelmuster. Die Uhrmacher polieren nun die Werkstücke von Hand und reinigen diese gründlich. „Das Polieren muss von Hand ausgeführt werden, da es viel Fingerspitzengefühl erfordert. Mit einer Maschine wäre das nicht möglich”, erklärt Ulrike Scheller. Mit bloßem Auge ist die Körnung der Polierstreifen nicht zu erkennen, denn sie beträgt in der Endstufe nur mehr einen Mikrometer. Bei Lehmann presst man schon jetzt die Lagersteine ein. Das erfolgt noch vor dem Rhodinieren, da die Lagersteine das Rhodium nicht annehmen und so verhindert wird, dass die Oberfläche Schaden nimmt. Erst danach folgt die eigentliche Galvanisierung in mehreren Bädern.
Vorbereitung: Die Werkstücke werden einzeln an einer leiterähnlichen Halterung aufgehängt und dann in die galvanischen Bäder eingetaucht
Copyright:48GradNord
Rainer Langenbacher
In diesem Falle handelt es sich um das Galvanisieren mit Rhodium, auch Rhodinieren genannt. Rhodium ist ein Nebenmetall von Platin und weist dessen gute Eigenschaften auf: es ist hart und robust, chemisch sehr beständig und glänzt sehr stark in heller Farbe. Das macht Rhodium zum perfekten Beschichtungsmetall, zum Beispiel von Weißgold. Denn Weißgold ist nichts anderes als durch Legierung "weiß" gemachtes Gelbgold, das durch den galvanischen Überzug mit Rhodium seine eigene schöne Farbe erhält. Eine solche Beschichtung ist sehr haltbar, kann allerdings nur sehr dünn aufgetragen werden.
Wie Uhrwerkteile galvanisiert werden
Beim Galvanisieren ist eine Metallverbindung in einem Salz- oder Säurebad gelöst. Das heißt, dass die Metallkationen im Elektrolyt vorhanden sind. Eine Anode und eine Kathode bilden Plus- und Minuspol des elektrochemischen Vorgangs. Als Minuspol (Kathode) dient der zu veredelnde Gegenstand. Wird Strom angelegt, schlagen sich positiv geladene Metallionen, die von der positiven Anode abgestoßen werden, auf den elektrisch leitenden Gegenstand nieder und überziehen ihn rundum gleichmäßig mit einer dünnen Schicht. Diese ist in der Regel etwa 0,001 bis 0,05 Millimeter dick. Dieser Vorgang findet immer in mehreren Bädern statt. Je nach gewünschter Härte und Schichtdicke sind sechs oder sieben Behandlungen erforderlich. Zwischen diesen Behandlungen und vor allem danach müssen die Teile gespült oder sogar die Entfettung wiederholt werden.Der letzte Schliff bevor die galvanisierten Teile zum Uhrwerk werden
Ganz am Schluss folgt noch einmal eine Feinreinigung durch Ultrabeschallung und mehrfache Spülung. Die letzte Spülung in entionisiertem Wasser ermöglicht schließlich eine fleckenfreie Trocknung. Danach brilliert das behandelte Objekt in neuem Glanz. Letztlich hängt die Qualität eines galvanischen Überzugs stets von der Qualität der Bäder und der Sorgfalt der einzelnen Arbeitsschritte ab. Ob absolute Sorgfalt beim Arbeiten angewandt wurde, zeigt das Entlacken der Lehmann-Brücken ganz zum Schluss.
Im Anschluss an die Galvanik muss der Schutzlack von den Werkstücken vorsichtig entfernt werden
Copyright:48GradNord
Rainer Langenbacher
Vertriebsleiterin Susanne Kleinig erzählt, wie nervenaufreibend es war, als zu Anfang nach dem Entlacken mit dem bloßen Augen kaum sichtbare Unsauberkeiten zum Vorschein kamen. „Das passiert, wenn kleinste Schmutzpartikel unter den Lack geraten”, erklärt Kleinig. „Leider sieht man erst ganz am Schluss, ob alle Arbeitsschritte vollkommen fehlerfrei waren.” Heute habe man aber die Produktion so weit optimiert, dass die Ausschussquote gering bleibe. „Eine Brücke durchläuft bis zu 25 Arbeitsschritte”, sagt Kleinig, „von der Herstellung des Rohlings, über das Fräsen, Gravieren, Polieren und mehrmalige Galvanisieren bis zum Entlacken.” Und Ulrike Scheller ergänzt: „Es ist etwas Besonderes, bei der Herstellung der Teile von Anfang an dabei zu sein und sie nicht nur zu montieren.” Doch nur absolute Perfektion in jedem Arbeitsschritt macht die Qualität der Galvanisierung bei Uhren am Ende aus.