Ein simples Band und doch so wichtig: Die Zugfeder – sie wird auch Werk- oder Triebfeder genannt – liefert die Antriebsenergie für das Uhrwerk. Eigentlich ist sie nicht mehr als ein elastisches, flaches Band aus einer Metalllegierung, welches schlicht als Biegefeder fungiert und spiralförmig aufgerollt ist. Durch das Aufziehen der Uhr wird die Zugfeder gespannt.
Die Zugfeder treibt das Räderwerk an
Wenn sie sich entspannt, treibt sie das Räderwerk an. Die Feder muss immer wieder zwischen Spannen und Entspannen wechselt. Dies gelingt 10.000- bis 20.000-mal praktisch ohne Verschleiß. Somit ist die Zugfeder ein außerordentlich guter, fast beliebig wieder aufladbarer Energiespeicher.
Das war nicht immer so: Die ersten Federn gab es im 15. Jahrhundert. Sie waren zunächst von Hand geschmiedet, später aus Draht gewalzt, spiralförmig aufgerollt und zuletzt in der Esse aufgekohlt oder angelassen, was sie zwar härter, aber auch spröder machte. Das Brechen der Feder galt daher jahrhundertelang als eine der häufigsten Pannen bei der Taschen- und später auch bei der Armbanduhr.
Heute sind Zugfedern nahezu bruchfest
Da Zugfedern weder ermüden, verbiegen, knicken noch abbrechen sollten und zudem Korrosion und Magnetismus trotzen sollen, spielen zeitgemäße Werkstoffe eine Rolle. Seit etwa 1965 haben struktur- und kaltgewalzte Legierungen die anfälligen Federspeicher aus Kohlenstoffstahl abgelöst. Bei ihnen treten die erwähnten Schwierigkeiten nur noch selten auf; etwa dann, wenn extrem ungünstige Temperatur-, Konstruktions- und Umgebungseinflüsse zusammenkommen.
Blick in die Fertigung: Bei Nivarox-FAR entstehen nicht nur Hemmungsteile. Die Swatch-Group-Tochter liefert auch Aufzugfedern und Federhäuser in Millionenstückzahlen.
PR
Zugfedern aus der Legierung „Nivaflex“, die heute bei hochwertigen Uhren am häufigsten verwendet wird, sind amagnetisch, bestechen durch extreme Zugfestigkeit bis zu 3.000 Megapascal, über 800 Vickers Härte, hohe Biegewechselfestigkeit, exzellente Korrosionsbeständigkeit und gute Temperaturbeständigkeit von –50 bis +350 Grad Celsius. Die Legierung besteht dabei aus 45 Gewichtsprozenten Kobalt, 21 Nickel, 18 Chrom, 5 Eisen, 4 Wolfram, 4 Molybdän, 1 Titan und 0,2 Beryllium; der Kohlenstoffanteil liegt unter 0,1 Prozent. Ein höherer Grad an Beryllium steigert die Festigkeits- und Härtewerte zusätzlich, was Miniaturisierungsanforderungen gerecht wird.
Neben den Werkstoffen hat sich die Form weiterentwickelt
Ein weiterer grundlegender Fortschritt zugunsten einer gleichmäßigen Kraftabgabe ist die heute gebräuchliche Form der Zugfeder: In ausgebautem Zustand nimmt sie eine S-Form an, das heißt, dass sie sich nach einigen Windungen in ihrer Richtung umkehrt und sich am anderen Ende im entgegengesetzten Drehsinn aufrollt. Diese Form entsteht, indem das äußere Ende nach einer Wärmebehandlung mit Hilfe einer kleinen Wickelmaschine entgegen dem Spiralverlauf aufgewunden wird. Die Vorteile bestehen unter anderem in einer gleichmäßigeren Spannungsverteilung über die gesamte Federlänge, mit der ein relativ konstantes Drehmoment einhergeht.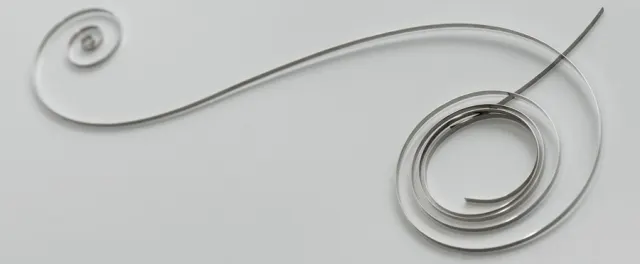
Zugfeder im Lieferzustand
PR
Der Interessierte bekommt dies beim Blick ins Uhrwerk jedoch nicht zu sehen: Die Feder verbirgt sich im Federhaus – einem flachen, dosenförmigen Gehäuse, das auf der einen Seite einen Zahnkranz trägt. In der Mitte hat es eine große Bohrung, die zur Lagerung des Federkerns, auch Federwelle genannt, dient. Verschlossen wird das Federhaus mit einem Deckel, der meist in eine Ausdrehung in der Wandung gepresst ist. Durch einen Haken, in den ein Loch am inneren Ende der Feder eingehängt wird, ist der Federkern mit der Feder verbunden. Von dort aus wird die Feder aufgezogen. Die Kraftabgabe erfolgt dann am äußeren Ende der Feder. Entspannt sie sich, legt sie sich an die Wandung des Federhauses, wobei dieses rotiert und das Räderwerk mit einer sehr langsamen Drehbewegung – etwa einer Umdrehung in sechs Stunden – antreibt.
Zugfedern sollen einen konstanten Drehmoment entwickeln
Zugfedern sollen bei einer minimalen Klingenstärke von bis zu 75 Tausendstelmillimetern ein hohes und vor allem möglichst konstantes Drehmoment entwickeln. Grundsätzlich wächst das Drehmoment der Federn linear mit ihrer Breite. Überproportional schlägt dagegen die Stärke der Klinge zu Buche: Eine doppelte Klingenstärke steigert das Drehmoment etwa um den Faktor acht. Bleibt die Länge der Zugfeder. Jedes Plus führt zu einer höheren Gangautonomie des Uhrwerks – das heißt, es läuft länger –, jedoch verringert sich das Drehmoment linear mit der Länge.Federhaus und Zugfeder sind bei der Kaliberentwicklung wichtig
Bei der Entwicklung eines neuen Kalibers spielen das Federhaus und das darin aufgewundene Speicherelement eine fundamentale Rolle. Weil bei klassischen Konstruktionen Stundenrad und Minutenrohr das Zentrum für sich beanspruchen, bestimmt der Platinenradius den maximalen Durchmesser des Federhauses. Seine Rotationsgeschwindigkeit definiert den Drehmomentsverlust in den ersten 24 Stunden nach Vollaufzug. Anschließend wird die Feder einer Handaufzugsuhr üblicherweise wieder komplett aufgewunden. Korrekt meint der oft falsch verwendete Terminus Gangreserve deshalb die darüber hinausreichende Zeit, bevor das Uhrwerk anhält. Die Zeit, die vom Vollaufzug bis zum Stehenbleiben verstreicht, nennt man dagegen Gangautonomie.Die Enden der Feder bei Automatik- und Handaufzugsuhren
Damit eine Zugfeder die gewünschten Eigenschaften erfüllt, kommt es neben den modernen Werkstoffen auch auf eine spezielle Konstruktion des Federendes und des Federzaums an. Letzterem kommt die Aufgabe zu, das äußere Ende des spiralförmig gewundenen Bandes an der Wandung des Federhauses zu halten. Der Zaum zwingt die Feder bei ihrer Entspannung auf der Federwelle in eine möglichst konzentrische Form. Die Reduktion der Reibung zwischen den Windungen ist ebenfalls ein wichtiger Aspekt.
Biegsam: Das Ende der Zugfeder wird zur Endkurve gebogen.
PR
Das äußere Ende der Feder unterscheidet sich – je nach Automatik- oder Handaufzugswerk. Bei Handaufzugswerken ist das Federende mit einem Endhaken oder Zaum (einer Handaufzugsbride) versehen, der sich bei Vollaufzug an der Federhauswandung einhakt. Automatikuhren verlangen nach einer anderen Lösung, da hier beim Tragen fortwährend Energie zugeführt wird. Eine starre Befestigung des Federendes an der Wandung des Federhauses ist nicht möglich. Bei Automatikuhren ist sie mit einer Bride beziehungsweise einer Schleppfeder ausgestattet, einem Stück aus besonders starkem Federstahl. Es wirkt als Rutschkupplung, da die Schleppfeder bei Vollaufzug im Federhaus nachrutscht. Beide Mechanismen verhindern, dass die Zugfeder überspannt wird. Sie ist also doch weit mehr als nur ein Stückchen flachgewalzter Draht.
Herstellung der Zugfedern
Den Anfang bei der Fertigung von Zugfedern macht das Walzen. Der weitaus günstigere, heute aber kaum noch verlangte Chromnickelstahl, wird bereits in Form von Bändern, Nivaflex als Runddraht geliefert. Dieser Runddraht wird in zahlreichen Vorgängen sehr dünn ausgewalzt. Besonders kompliziert ist dabei, dass ein gleich mehrere Kilometer langes Metallband auf seiner gesamten Länge eine gleich bleibende Stärke aufweisen muss. Noch schwieriger gestaltet sich dies bei modernen Zugfedern, da diese im Querschnitt eine leichte Wölbung aufweisen.
Walzen: Am Anfang wird runder Draht in mehreren Gängen flachgewalzt. Nach jedem Arbeitsschritt wird das gewalzte Band erneut auf eine Spule aufgewickelt.
PR
Nach der erforderlichen Stärke geht es um eine exakte Breite, welche durch Schleifen erzielt wird. Ist in Stärke und Breite das gewünschte Maß exakt erreicht, werden vom Federband Stücke in der benötigten Länge gestanzt. Diese sind in der Regel 400 bis 500 Millimeter lang – das richtet sich ganz nach dem Uhrwerk. Zum Beispiel macht die Feder bei einem bekannten Standardkaliber wie dem ETA 2892 acht bis zehn Touren. Gleichzeitig erfolgt das Stanzen eines Lochs zur Aufnahme des Federkernhakens und das Biegen dieses Federendes zum „Coquillon", einer Schlaufe, die sich fest um den Federkern legen wird. Durch eine Wärmebehandlung erhält die Feder ihre gewünschte Form und Elastizität. Schließlich wird die Bride (Automatik- oder Handaufzugsbride) angeschweißt.
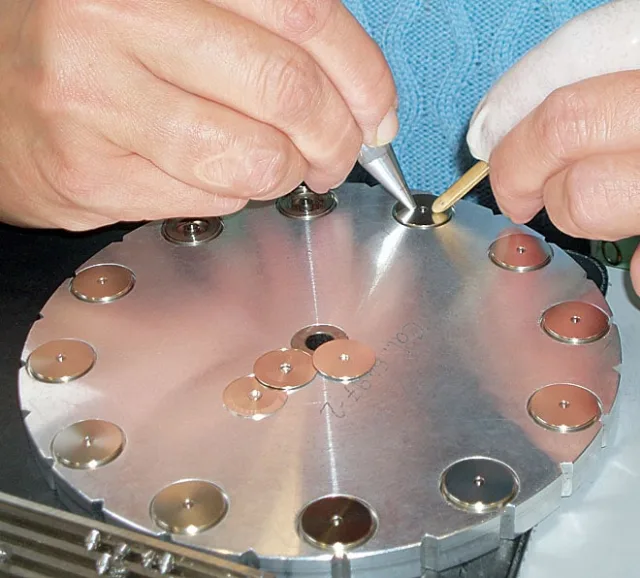
Manuell: Bei Federhäusern für hochwertige Uhrwerke erfolgt das Einsetzen der Achse und das Verschließen des Federhauses von Hand.
PR
Je nach Kundenwunsch werden die aufgerollten Zugfedern dann in Ringe aus Kunststoff oder Aluminium eingespannt oder fix und fertig in ein – stets vom Kunden angeliefertes – Federhaus eingezogen. Zuvor wird die Oberfläche der Feder mit einer speziellen Gleitschicht versehen; außerdem wird hoch präzise durch eine Maschine ein Spezialfett an die Wandung des leeren Federhauses aufgebracht. Mit Hilfe kleiner Maschinen werden die Federn dann in das Federhaus aufgezogen, die Achse eingesetzt und das Federhaus geschlossen. Dabei müssen Achse und Feder in der Höhe genaues Spiel haben.

Fertig: Federn – hier für ein Handaufzugswerk – werden für die Auslieferung in Ringe aufgezogen.
PR
Eine gleichförmige Antriebskraft sowie eine hohe Gangautonomie stellen heute für Uhrmacher eine besondere Herausforderung dar. Die Unruhfrequenz spielt bei allen Berechnungen eine wesentliche Rolle. Mit wachsendem Tempo sinkt in der Regel auch die Gangautonomie. Bis zu einer Woche erbringen ausgeklügelte Konstruktionen mit nur einem Federhaus. Das belegt beispielsweise eine 1913 lancierte Uhr der Firma Hebdomas, deren Federhaus das gesamte Uhrwerk überdeckte. Ein ähnliches Konstruktionsprinzip wendete Ulysse Nardin beim Modell Freak an.

Bei der Freak von Ulysse Nardin bedeckt die Aufzugsfeder das gesamte Uhrwerk
PR
Die 1930er Jahre brachten Acht-Tage-Uhrwerke mit Standardfederhaus, modifizierter Getriebekette sowie winziger Unruh, Frequenz 2,5 Hertz. Heutige Vier-Hertz-Schnellschwinger laufen meist 72 Stunden am Stück. Sie stellen die Zeit also auch nach einem Wochenende im Tresor noch weitgehend präzise dar. Dass sich die Verwendung eines einzigen Federhauses, 28.800 stündliche Halbschwingungen und eine Woche Gangautonomie nicht ausschließen, belegt IWC mit den Manufakturkalibern 51011, 51111 und 59210.
Paralleler Antrieb mit zwei Federhäusern
Die Verteilung der Antriebskraft auf zwei Zugfedern ist keineswegs neu. Henri Louis Jaquet-Droz wendete diesen Kunstgriff bereits 1785 an. Auch Abraham-Louis Breguet beschäftigte sich ausgiebig mit der energetischen Optimierung seiner Chronometer. Zwei gleichzeitig auf ein Minutentrieb einwirkende Federhäuser ersetzten nicht nur das übliche System aus Kette und Schnecke, sondern ermöglichten auch eine Halbierung der Klingenstärke. Bei Armbanduhren machte die Manufaktur Favre-Leuba 1962 durch die drei Millimeter hohen Kaliberfamilien 25x und 27x von sich reden. Beide wurden per Hand aufgezogen und verfügten ähnlich der Breguet’schen Entwicklung über zwei auf das Minutentrieb einwirkende Federhäuser. Beeindruckend ist die Klingenstärke von nur 0,05 Millimetern, die schon damals 9¼ Federhausumdrehungen und rund 40 Stunden Gangautonomie ermöglichte. Die Vorteile bestehen in einer Reduktion des einseitigen Lagerdrucks auf das Minutenrad. Zudem bringen dünnere Zugfedern eine gleichförmigere Kraftentfaltung mit sich. Andererseits nimmt bei einer solchen Parallelschaltung und dem gemeinsamen Einwirken auf das zentrale Trieb die Bauhöhe zu.Seriell geschaltete Federhäuser
Einen anderen Weg schlug Alfred Helwig ein. Der Glashütter Uhrmacher setzte auf zwei hintereinander, also seriell geschaltete Federhäuser. In diesem Fall spannt die erste Zugfeder bei Vollaufzug das nachfolgende Pendant. Es ergibt sich also eine Verdopplung der Federlänge. Dieses Prinzip wendete Longines ab 1975 bei der Kaliberfamilie 89x mit zwei übereinander angeordneten Federhäusern an. Wesentlich flacher war das Folgekaliber L990 mit zwei nebeneinander positionierten Federhäusern.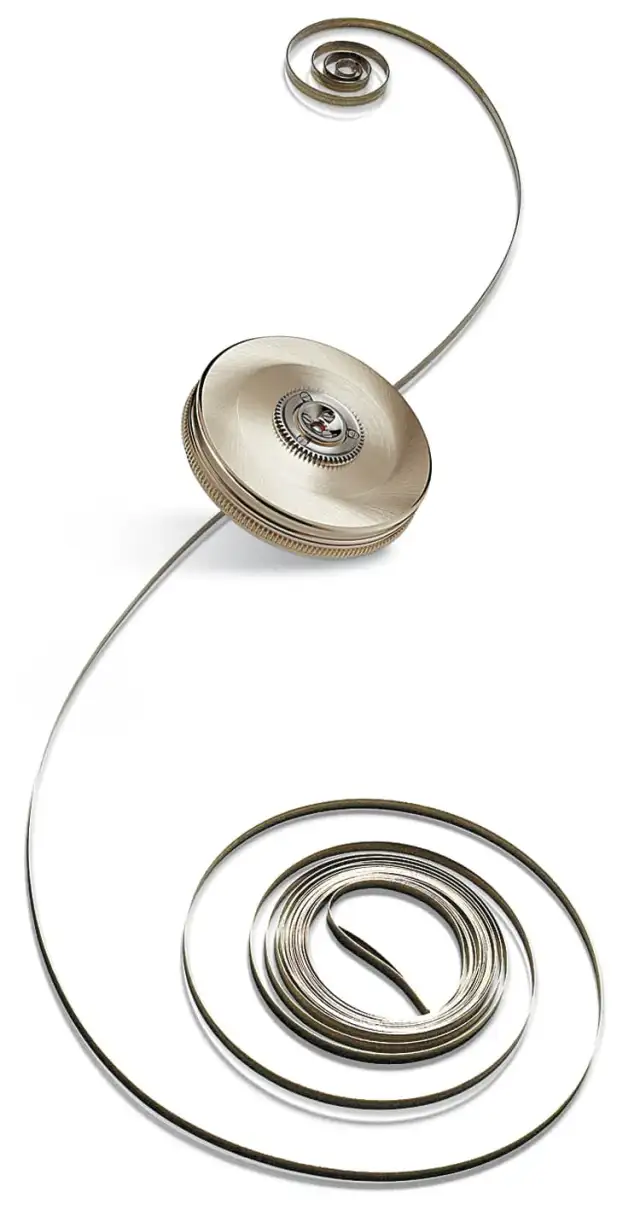
Mit einer besonders langen Feder erreicht A. Lange & Söhne 31 Tage Gangautonomie
PR
Hier zeigten sich die Vorteile eines Duos schnellrotierender Energiespeicher: Durch die niedrigeren Drehmomente ließ sich die auf das Räderwerk ausgeübte Kraft reduzieren und die Leistung trotzdem steigern. Bei Automatikwerken kann der Aufzugsmechanismus effizienter agieren. Nicht zuletzt deshalb ist dieses Prinzip in neuen Konstruktionen immer häufiger zu finden. Die Addition der Zugfederlängen wirkte sich zudem positiv auf die Gangautonomie aus. Je nach Auslegung liefen diese Kaliber zwei oder acht Tage. Den Gipfel erreichte A. Lange & Söhne mit dem Kaliber L.034.1 des Modells Lange 31, das 31 Tage ohne Energienachschub auskommt.

Acht Tage lang läuft das Panerai-Kaliber P.2002 dank dreier Federhäuser
PR
Drei, vier und sogar noch mehr Federhäuser
Ganze drei Federhäuser in serieller Anordnung verbaut etwa Panerai in den Kalibern P.2002, P.2003 und P.2004. Der Lohn sind mindestens acht Tage Gangautonomie. Blancpain zog bei den Automatikkalibern 5235DF und 6938 mit jeweils 192 Stunden Gangautonomie nach. Chopard verpackt in der L.U.C Quattro ein richtiges Federhausquartett: Viermal 470 Millimeter Zugfeder verleihen dem Kaliber L.U.C 1.98 eine Gangautonomie von mindestens 216 Stunden oder neun Tagen. Gleich 14 Tage lang läuft das Tourbillonkaliber 2253 von Vacheron Constantin. TAG Heuer hingegen belässt es beim Kaliber V4 mit linearem Selbstaufzug und Riemenantrieb bei lediglich 52 Stunden.
Auf der Rückseite des TAG-Heuer-Kalibers V4 sind die vier Federhäuser zu erkennen
PR
Eidgenössischer Uhrmacherkompetenz in Person von Enrico Barbasini, Michel Navas und Mathias Buttet bediente sich die amerikanische Uhrenmarke Jacob & Co. beim Handaufzugstourbillon The Quenttin: Die nicht mehr existente BNB Concept SA hob das Kaliber 5 mit drei Hertz Unruhfrequenz, sieben nebeneinander stehenden Federhäusern und 31 Tagen Gangautonomie aus der Taufe. Weitaus wichtiger als immer mehr Zugfedern dürfte die technische Evolution der Energiebündel sein. Mit vier normal dimensionierten, polymer beschichteten Zugfedern aus glasfaserverstärktem Kunststoff und einem auf Energieeffizienz bedachten Gesamtkonzept erreicht Cartier bei seiner neuesten Konzeptuhr ID-Two, die in der letzten Chronos-Ausgabe ausführlich vorgestellt wurde, mehr als einen Monat Gangautonomie.

Das Modell The Quenttin von Jacob & Co. bricht mit sieben Federhäusern alle Rekorde
PR