Zur Werkeproduktion von Rolex in Biel erhält normalerweise kein Aussenstehender Zutritt. Chronos aber war da und verfolgte das Werden des Daytona-Kalibers 4130 (Artikel aus Chronos 4.2010).
Der Ort, an dem Rolex seine gut 750.000 Werke pro Jahr fertigt, ist ein gigantischer Komplex aus vier riesigen Gebäuden am Stadtrand von Biel.
Zuerst fällt die schiere Größe auf. Der Ort, an dem Rolex seine Werke baut, ist ein gigantischer Komplex, gelegen am Stadtrand von Biel. Er besteht aus vier riesigen imposanten Gebäuden, die 170000 Kubikmeter Raum einnehmen. Auf den ersten Blick wirken sie wie eine uneinnehmbare Festung.
Für uns, zwei Redakteure von Chronos’ US-Schwestermagazin WatchTime, ist es etwas Besonderes, hier zu sein. Denn Rolex gewährt zu seiner Werkefertigung in Biel normalerweise keinen Eintritt, auch nicht für Fachjournalisten. Für diesen Februarnachmittag aber hat uns das Unternehmen eine Tour durch die Produktion ermöglicht. Wir sehen, wie die gut 750.000 Werke pro Jahr hergestellt werden – von der Grundplatine bis zur Spiralfeder.
Bevor wir starten, führt man uns zur Einstimmung einen Film vor. Gezeigt wird er in einem verhältnismäßig großen Vorführraum, der sich an den größten Empfangsbereich anschließt, den wir je gesehen haben: ein zwei Stockwerke hohes, lichtdurchflutetes Atrium mit einem Rolex-grünen Marmorboden.
Diese im Bieler Industriegebiet Champs-de-Boujean gelegene „Manufacture des Montres Rolex SA“ ist ein Schwesterbetrieb der Rolex SA in Genf, in der Gehäuse, Armbänder und Zifferblätter hergestellt, Steine gesetzt und Werke in Gehäuse eingeschalt werden (siehe „Rolex von innen“, Chronos 5-2006).
Hier in Biel fertigen rund 2.000 Mitarbeiter Werkkomponenten (50 Millionen pro Jahr), bauen die Werke zusammen und schicken sie zur offiziellen Schweizer Chronometerprüfstelle COSC. Rolex ist bekannt dafür, fast alle seine Werke als Chronometer zertifizieren zu lassen; eine Ausnahme bilden die meisten Cellini-Modelle (Cellini Prince kommt allerdings mit Chronometerzeugnis). Wenn die Werke von der COSC zurückkommen, schickt Rolex sie von Biel nach Genf zum Einschalen. Die vier eingangs erwähnten Gebäude heißen Rolex III, IV, V und VI – Rolex I und II, alte Fabrikgebäude nahe der Innenstadt, gehören nicht mehr zur Firma. Dafür besitzt Rolex aber noch eine Fabrik mit 150 Angestellten in Le Locle, wo ein kleinerer Teil der Werkeassemblage stattfindet.
Bis 2004 hatten Rolex Biel und Rolex Genf unterschiedliche Eigentümer: Biel gehörte den Nachkommen von Jean Aegler, dessen Bieler Fabrik Aegler SA den Rolex-Gründer Hans Wilsdorf seit 1905 mit Werken belieferte. Rolex Genf war und ist im Besitz der Hans Wilsdorf Stiftung, die Wilsdorf 1945 gründete. Vor sechs Jahren wurde Biel von Genf übernommen. Die beiden Unternehmen, die sich vorher mitunter in herzlicher Abneigung zugetan, gleichzeitig aber auf Gedeih und Verderb aufeinander angewiesen waren, verschmolzen miteinander. Da Rolex in den letzten Jahren auch viele weitere Zulieferer übernommen und integriert hat, ist das Unternehmen heute, wie es im Fachjargon so schön heißt, vertikal integriert; eine Firma mit einer beeindruckenden Fertigungstiefe.
Der Film ist zu Ende, wir starten unseren Rundgang. Er soll uns, so erklärt es François Paschoud, einer der technischen Direktoren, die Produktion des Daytona-Kalibers 4130 Schritt für Schritt nahebringen. Rolex lancierte das Kaliber 4130 im Jahr 2000, um das bis dahin verwendete Kaliber 4030 zu ersetzen, das auf dem Zenith El Primero basierte. Für Rolex war das eine wichtige Zäsur, denn seitdem verwendet Rolex für seine Uhren ausschließlich in-house gefertigte Werke.
Neben Paschoud begleiten uns Raymond Kerrison, der Direktor von Rolex Biel, und Entwicklungschef Jacques Baur.
Wir starten in Rolex V, wo Platinen und Brücken produziert werden. Dort, in einem höllisch lauten Raum, sieht es aus, als seien Außerirdische gelandet: Da steht ein Dutzend riesiger runder, UFO-artiger Glaskapseln, die fast bis zur Decke reichen und vielleicht drei, vier Meter Durchmesser haben. Die Rolex-Verantwortlichen nennen sie „Module“. Manche sind an ihrer Spitze über Metallschienen mit einem benachbarten Modul verbunden. Diese Schienen, so erfahren wir bald, sind eine Art Transportsystem, mit dem Komponenten von einem Modul zum nächsten gebracht werden. Vier Module arbeiten fürs 4130. In jedem befinden sich CNC-Maschinen, die die in einer anderen Abteilung vorgestanzten Platinen durch Bohren, Fräsen, Drehen und Polieren weiter bearbeiten. Von außen sieht man praktisch nichts, außer dem Öl, das literweise über die Platinen und Brücken fließt, um Metallspäne wegzuspülen. Über 50 Werkzeuge arbeiten gleichzeitig in den vier Modulen; das, was sie tun, kann man auf Monitoren beobachten. Menschen gibt es in diesem Raum wenige – nur ein oder zwei Arbeiter werden benötigt, um die Maschinen am Laufen zu halten.
Ufos und unterirdische Gänge
Die Module werden eigens für Rolex gebaut; von einer Firma, die ebenfalls zum Unternehmen gehört. Sie erfüllen verschiedene Zwecke. In erster Linie sind sie dazu da, damit das Öl nicht überall herumspritzt. Außerdem schützen sie vor Staub und sorgen für gleichbleibende Temperaturen, sodass sich die bearbeiteten Teile nicht ausdehnen oder zusammenziehen können. Das hätte bei Toleranzen von zwei Tausendstelmillimetern verheerende Folgen.
Wenn ein Modul mit seiner Arbeit fertig ist, wird das bearbeitete Teil zum nächsten befördert. Keine menschliche Hand berührt es während dieser Produktionsphase. Der gesamte Prozess besteht aus rund 100 Schritten, von denen einige nebenan, in Rolex III, erfolgen. In der Zwischenzeit gehen wir durch die Qualitätskontrolle, wo die Platinen und Brücken von mehreren Mitarbeitern nochmals ausgemessen und überprüft werden. Sie sitzen hinter einer Glaswand, in einer kontrollierten Atmosphäre, denn auch für die Messungen sind konstante Temperaturen unverzichtbar. Haben die Teile die Kontrolle überstanden, werden sie rhodiniert und dekoriert.
Anschließend gehen wir durch einen unterirdischen Gang, der Rolex V mit Rolex IV verbindet, wo Kleinteile wie Räder, Wellen, Unruhreifen sowie die Microstella-Schrauben für die Unruh produziert werden. Auf dem Weg dorthin kommt uns ein Mann auf einem Fahrrad entgegen. Am Aufzug von Rolex IV stehen noch mehr Fahrräder, alle mit hellen Reifen, mit denen Mitarbeiter schnell von einem Gebäude zum anderen kommen können.
In dieser Abteilung werden lange Metallstangen, manche bis zu zwei Meter lang, in kleine Teile geschnitten, manche von ihnen nur einen Millimeter dick. Die Toleranzen liegen wieder im Zwei-Mikron-Bereich.Auch hier kommen, wie zuvor bei den Brücken und Platinen, CNC-Maschinen zum Einsatz, auch hier sieht man nicht viel von außen. Das Metall, eine Stahl-, Kupfer- oder Aluminiumlegierung, wird auf der einen Seite zugeführt, auf der anderen kommen, wie durch ein Wunder, kleine Schräubchen oder Zahnräder heraus. Auch dekoriert wird hier: Zum Beispiel erhalten bestimmte Räder einen Sonnenschliff.
Die blaue Parachrom-Spirale
All diese Teile finden zusammen in Rolex VI, zu dem wir durch einen anderen unterirdischen Gang gelangen. Doch bevor wir die Abteilung Werkassemblage betreten, dürfen wir uns etwas ansehen, was selbst weitgereiste Uhrenmanufakturbesucher nur selten zu Gesicht bekommen: die Herstellung von Spiralfedern. Hier also stellt Rolex seine berühmten blauen Parachrom-Spiralen her! Das Kaliber 4130 war das erste, in dem die Parachrom-Spirale eingesetzt wurde, zehn Jahre ist das jetzt her. Mittlerweile wird sie in allen Oyster-Herrenmodellen eingesetzt; für die Cellini-Modelle und die Damenuhren wird nach Aussage von Rolex eine mit Nivarox identische Legierung benutzt.
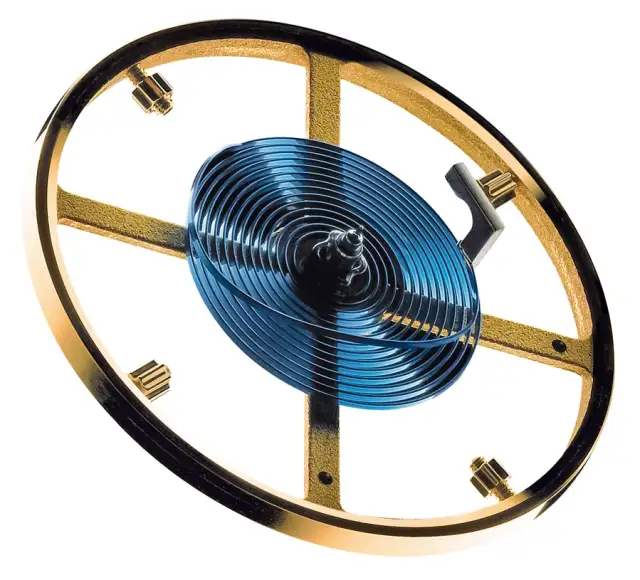
State of the art: Rolex-Unruh mit blauer Parachrom-Spirale und vier „Microstella“-Schrauben
Rolex
Die Vorteile der Parachrom-Spirale, sagt Jacques Baur, liegt in ihrer besonders guten Unempfindlichkeit gegen Stöße und in ihren antimagnetischen Eigenschaften. Es gibt zwei Arten von Parachrom-Spiralen: eine für die Kaliber 4130 und 4160 (die komplizierte Schwester des 4130 für die Yacht-Master II) und eine für die Nicht-Chronographen-Kaliber der Serie 3100, die für Herrenuhren wie GMT-Master II, Submariner, Deepsea, Day-Date, Datejust, Explorer und Milgauss verwendet werden.
Die Parachrom-Legierung besteht zu 85 Prozent aus Niob und zu 15 Prozent aus Zirkonium. Rolex fertigt sie selbst: Dabei werden 30 Zentimeter lange Stangen von jedem Material zusammengeschmolzen, immer zweimal Niob und einmal Zirkonium.
Geschmolzen wird in einem Vakuum-Schmelzofen, einem großen, glänzenden Ungeheuer, das bis durch die Decke reicht und wie ein dickliches Raumschiff aussieht. So einen Ofen gibt es nur bei Rolex. Wir dürfen auch mal hineinschauen. Dafür müssen wir eine Plattform besteigen und eine dunkle Schutzbrille aufsetzen, dann spähen wir durch ein Bullauge und sehen eine glühende Stange, aus der schließlich Parachrom werden soll, durch einen brennenden Elektronenstrom auf eine Temperatur von 2.400 Grad erhitzt. Die Stange wird insgesamt dreimal durchs Elektronenfeuer geschickt, bis die Metalle vollständig miteinander verschmolzen sind. All das geschieht vollautomatisch; ein Techniker beobachtet lediglich am Bildschirm, dass alles ordnungsgemäß abläuft.
Sobald das Parachrom fertig ist, wird es zu Spiralfedern verarbeitet.
Dabei wird das Material immer wieder gezogen und flach gewalzt und dazwischen mehrmals thermisch behandelt, sodass es sich „entspannt“ und sich besser bearbeiten lässt.
Schließlich ist die ursprünglich 30 Zentimeter lange und einen Zentimeter dicke Stange drei Kilometer lang und etwa 0,1 Millimeter dick – der exakte Durchmesser variiert je nach Art der Spirale. Aus einer einzigen Stange entstehen so 10.000 Spiralfedern.
Als erstes wird das Material kaltgewalzt. Das besorgen zwei Mitarbeiter, die auf beiden Seiten der Walzmaschine stehen. Sie zwingen die immer dünner werdende Stange vor und zurück durch immer kleinere Löcher. In dieser Hi-Tech-Umgebung wirken die beiden Männer wie ein Anachronismus. Der Grund, warum für diese spezielle Aufgabe Mitarbeiter aus Fleisch und Blut eingesetzt werden, liegt laut Baur darin, dass das Metall relativ brüchig ist, wenn es aus dem Schmelzofen kommt. Es muss höchst vorsichtig behandelt werden, bis es eine gewisse Elastizität erreicht. Wenn die Arbeiter fertig sind, ist die Stange drei Meter lang.
Den nächsten Schritt, das Drahtziehen, besorgen wieder Maschinen. Wir beobachten eine Maschine dabei, wie sie den Draht durch vier aufeinanderfolgende Pressformen zieht. Der Draht muss durch insgesamt 50 dieser Formen und wird dabei immer dünner. Anschließend wird der immer noch runde Draht durch das sogenannte Kaltwalzen abgeflacht. Der temperaturkontrollierte Raum, in dem das geschieht, ist unzugänglich. Baur erklärt, warum: Die Temperaturveränderung, die unser Eintreten zur Folge hätte, würde den Draht zerstören. Hier geht es um Toleranzen von 0,1 Mikron. Beim Blick durch die Scheibe können wir den Draht mehr erahnen als sehen: Er ist jetzt 50 mal 150 Mikron dick.
Schließlich wird der gerade Draht in eine Spiralfeder verwandelt. Das Verfahren dazu heißt auf Französisch „estrapadage“. Eine Mitarbeiterin nimmt drei je 20 Zentimeter lange Drahtabschnitte und fädelt je ein Ende, mit einer beeindruckenden Behendigkeit, durch ein winziges Löchlein in eine Form ein und befestigt die einzelnen Stränge in der Mitte, sodass sie fixiert sind. Danach lässt sie die Form wie eine Töpferscheibe rotieren, sodass die drei Drähte sich um die Spindel im Innern der Form winden. Der Grund dafür, dass man drei Drähte zusammen aufwickelt, liegt Baur zufolge daran, dass so die richtige Krümmung und der genaue Abstand zwischen den Windungen sichergestellt wird. Abschließend wird die Form erhitzt, damit die Drähte ihre neue Gestalt behalten. Mit einer Pinzette trennt die Mitarbeiterin die drei Spiralfedern, deren Durchmesser rund sechs Millimeter misst. So schwierig schon das Biegen ist: Das Trennen, so Baur, ist eine noch heiklere Aufgabe – man braucht nur leicht mit der Pinzette abzurutschen, und schon sind die Spiralen kaputt.
Die Spiralen haben eine schöne kobalt- oder königsblaue Farbe, ähnlich wie gebläute Schrauben oder Zeiger. Die Farbe kommt durch einen Oxidationsprozess zustande, erfahren wir. Der macht die Spiralen nicht nur schöner, sondern auch stabiler – stabiler in dem Sinne, dass sie über einen langen Zeitraum hinweg zuverlässig und unverändert arbeiten. Das Bläuen selbst zeigt man uns nicht: Es zählt zu den Geheimnissen von Rolex.
Was wir dagegen sehen dürfen, ist einer der letzten Schritte der Spiralfederherstellung: das Hochbiegen des äußeren Endes zu einer Breguetspirale. Das geschieht vollautomatisch, durch eine weitere dieser Maschinen, die es nur bei Rolex gibt. Sie besitzt zwei flache Hämmer, die an genau definierten Stellen auf die Spirale schlagen, um die im gewünschten Winkel zu biegen. Ganz ohne das menschliche Auge geht es dann freilich doch nicht: Da jede Parachromspirale leicht von der anderen abweicht und so jeweils anders auf die Hammerschläge reagiert, überprüft eine Angestellte durch ein Mikroskop, ob jede Endkurve die richtige Krümmung besitzt. Falls nötig, kann sie mithilfe der Maschine manuell „nachhämmern“.
Assemblage: Der Zusammenbau der Werke
Jetzt ist es an der Zeit zu sehen, wie sich alle Einzelteile zum Kaliber 4130 zusammenfügen. Wir gehen zur sogenannten „T1“, dem Zusammenbauen der Werke. Hier ist jeder Arbeiter auf bestimmte Schritte spezialisiert: Einer setzt die Getriebekette zusammen, ein anderer setzt die Unruh ein und schraubt die Unruhbrücke fest – mit einem elektrischen Schraubendreher, der darauf eingestellt ist, die Schrauben mit dem gewünschten Drehmoment anzuziehen. Langsam sehen wir das 4130 werden: Seine blaue Spiralfeder beginnt zu atmen: Sie dehnt sich aus und zieht sich zusammen.
Um die Uhrwerke während der Montage vor Staub zu schützen, laufen sie – jeweils zehn an der Zahl – auf einem horizontal rotierenden Karussell unterhalb des Uhrmachertisches. Nur das, an dem gerade gearbeitet wird, erscheint durch ein Loch in der Tischplatte vor den Händen des bearbeitenden Uhrmachers. Danach wird es wieder heruntergefahren, und das nächste kommt nach oben.
Der nächste Schritt ist das Ölen. Auch das geschieht maschinell. Auf einem Bildschirm verfolgen wir, wie winzige Tröpfchen auf jeden Zahn des Ankerrads gegeben werden. Insgesamt gibt es 200 Stellen im Werk, die geschmiert werden müssen. Rolex verwendet fünf Sorten an Ölen und Fetten für jedes Kaliber. So gibt es beispielsweise ein spezielles fürs Federhaus, ein anderes für den Chronographenmechanismus. Einige der Schmiermittel stellt Rolex selbst her, andere bezieht man von Lieferanten, die dazu spezielle Rolex-Rezepturen benutzen. Baur erzählt uns, dass die Belastung, der einige Komponenten ausgesetzt sind, im Verhältnis zur Größe vergleichbar ist mit der Beanspruchung einer Eisenbahnschiene durch den Zug. Doch so wichtig die Öle auch sind: Sie werden fast als Spurenelemente verabreicht. Pro Jahr verbraucht Rolex gerade mal zehn Liter Öl für alle Werke, die es produziert und für die, die zum Service kommen.
Ziel Chronometer: Die Regulierung
In der folgenden Abteilung werden die Werke reguliert. Ziel ist es, die Chronometerstandards der COSC zu erreichen, die einen Nachgang von höchstens vier und einen Vorgang von maximal sechs Sekunden pro 24 Stunden gestatten. Mit einem winzigen Schraubenschlüssel bewegt eine Uhrmacherin die goldenen Microstellaschrauben – sie heißen so wegen ihrer Sternform –, um die Unwucht zu optimieren. Jede Unruh hat vier davon.
Jetzt läuft das Werk hochpräzise. Aber etwas fehlt noch: Es ist noch kein Chronograph. Das ändert sich schon bald, als eine andere Uhrmacherin sich daran macht, die Chronographenteile auf die Basis zu montieren. Mit einer nadelfeinen Pipette ölt sie acht Stellen des Chronographenmechanismus. Anschließend schraubt sie die Chronographenbrücke auf und überprüft durch Starten und Stoppen des Chronos, ob alles wie gewünscht funktioniert.
Das fertige Werk schickt Rolex zur COSC; entweder nach Biel oder ins Genfer Büro der Prüfstelle. 2008 hat Rolex insgesamt exakt 769.850 Werke durch die offizielle Schweizer Chronometer-Kontrollstelle zertifizieren lassen.
Jetzt fehlt noch eine Station. Vom Restaurant im obersten Stockwerk von Rolex VI blicken wir durch das Panoramafenster auf ein riesiges Bauprojekt: das künftige Rolex VII. 2012, wenn es fertig ist, hat Rolex hier weitere 230.000 Kubikmeter zur Verfügung. Unterbringen wird man dort unter anderem ein robotergestütztes Komponentenlager und Transportsystem, das die benötigten Einzelteile innerhalb von Minuten zu den wartenden Arbeitsplätzen befördert – ähnlich, wie es das auch bei Rolex Genf gibt. Der Erweiterungsbau wird mit Rolex IV und VI zu einer gigantischen Produktionseinheit verbunden sein. Riese Rolex wird noch größer.
Text: Norma Buchanan
Aus Chronos 4.2010
Artikel:
Bei Rolex in Genf Alles weitere Wissenswerte über Rolex erfahren Sie im 155-seitigen Chronos Spezial Rolex, das Sie in der Chronos-iPad-App herunterladen können: https://itunes.apple.com/de/app/chronos-watch/id406162886?mt=8